先锋PIONEER DRM-3000电路图
)
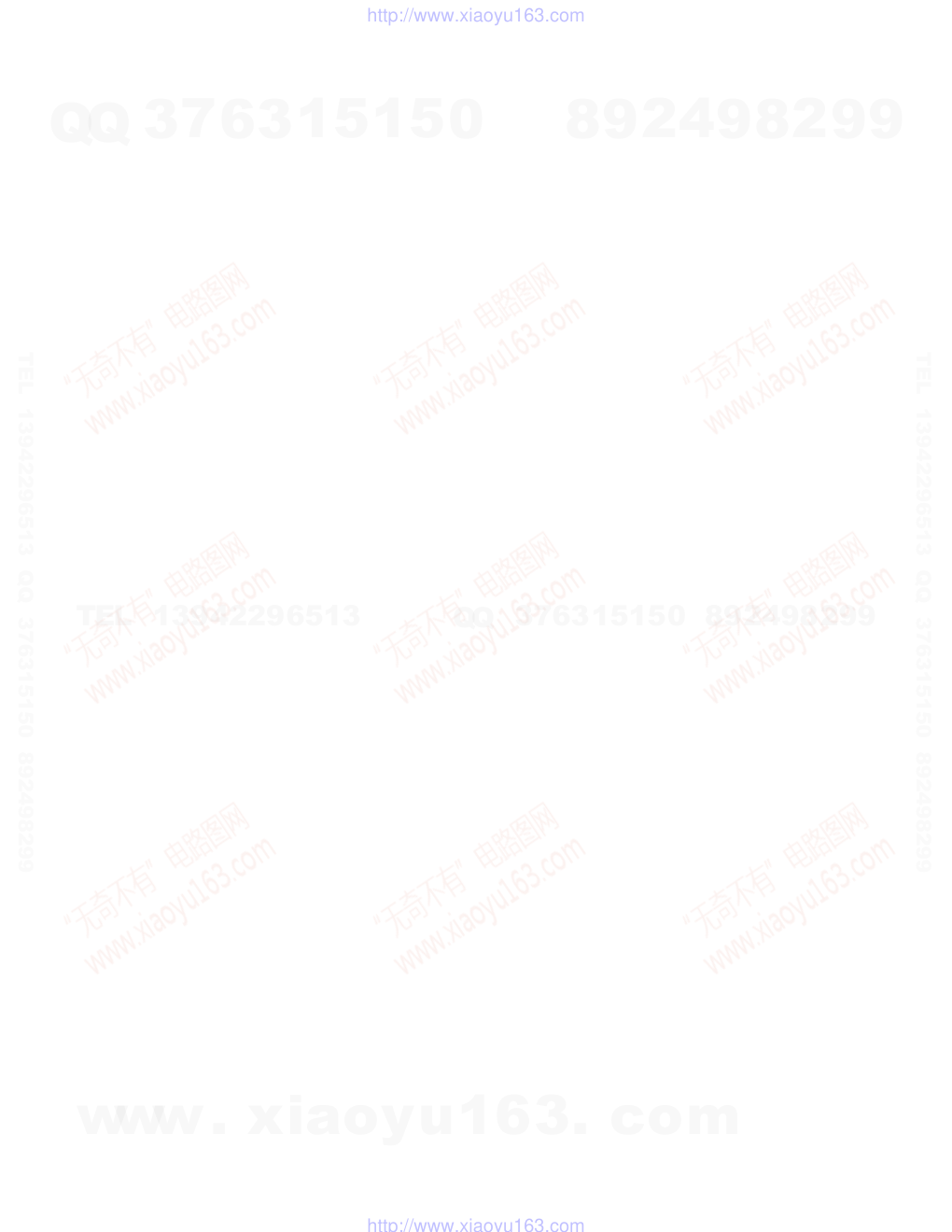)
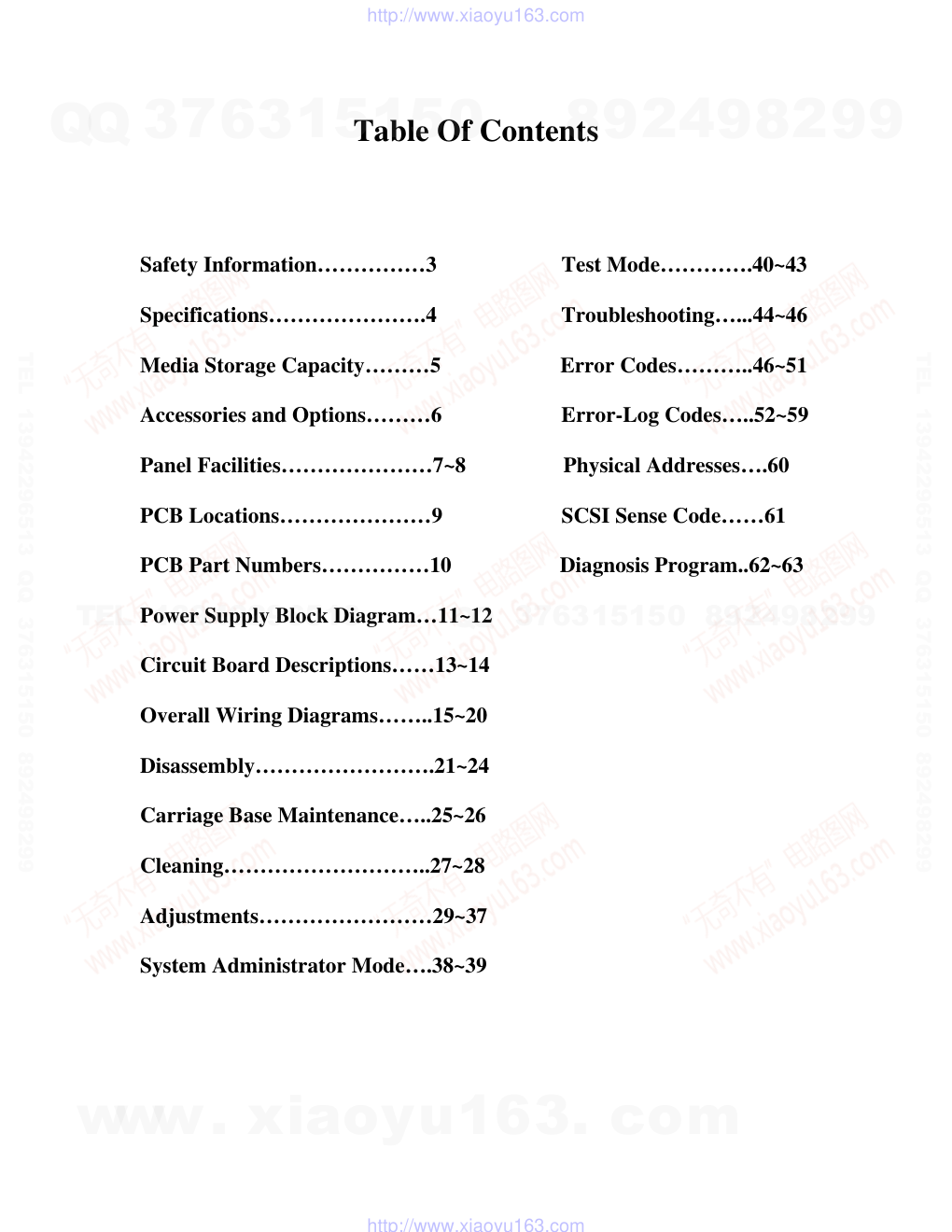)
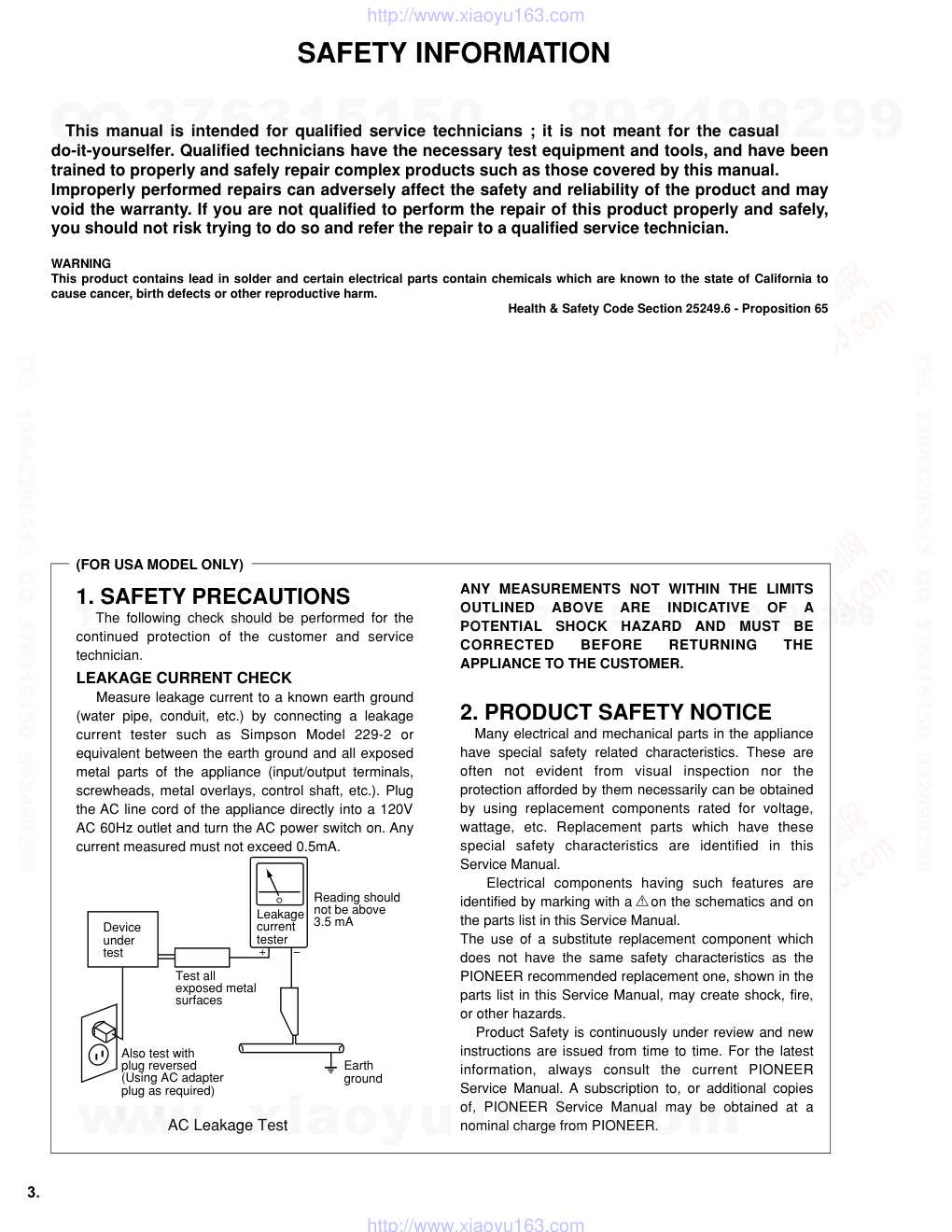)
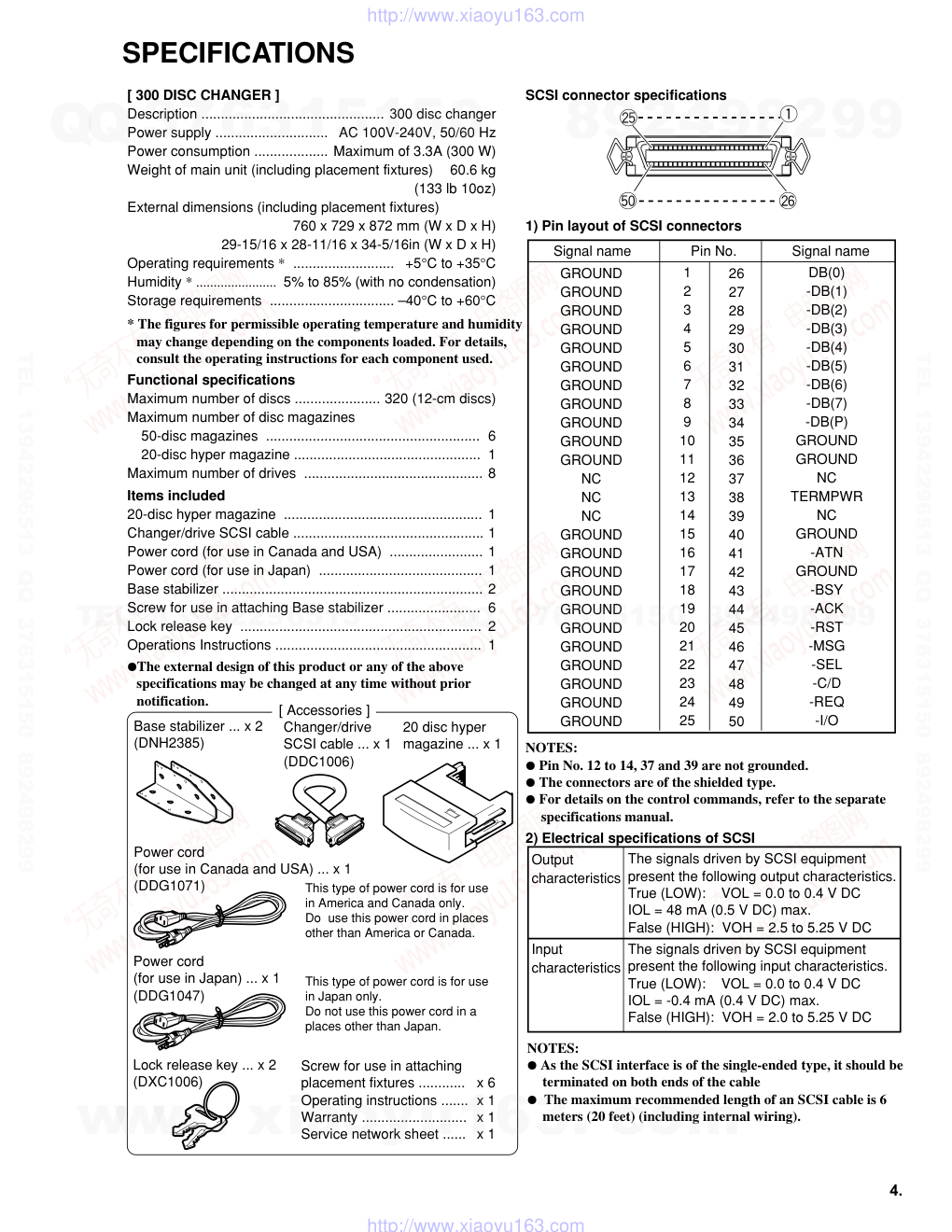)
)
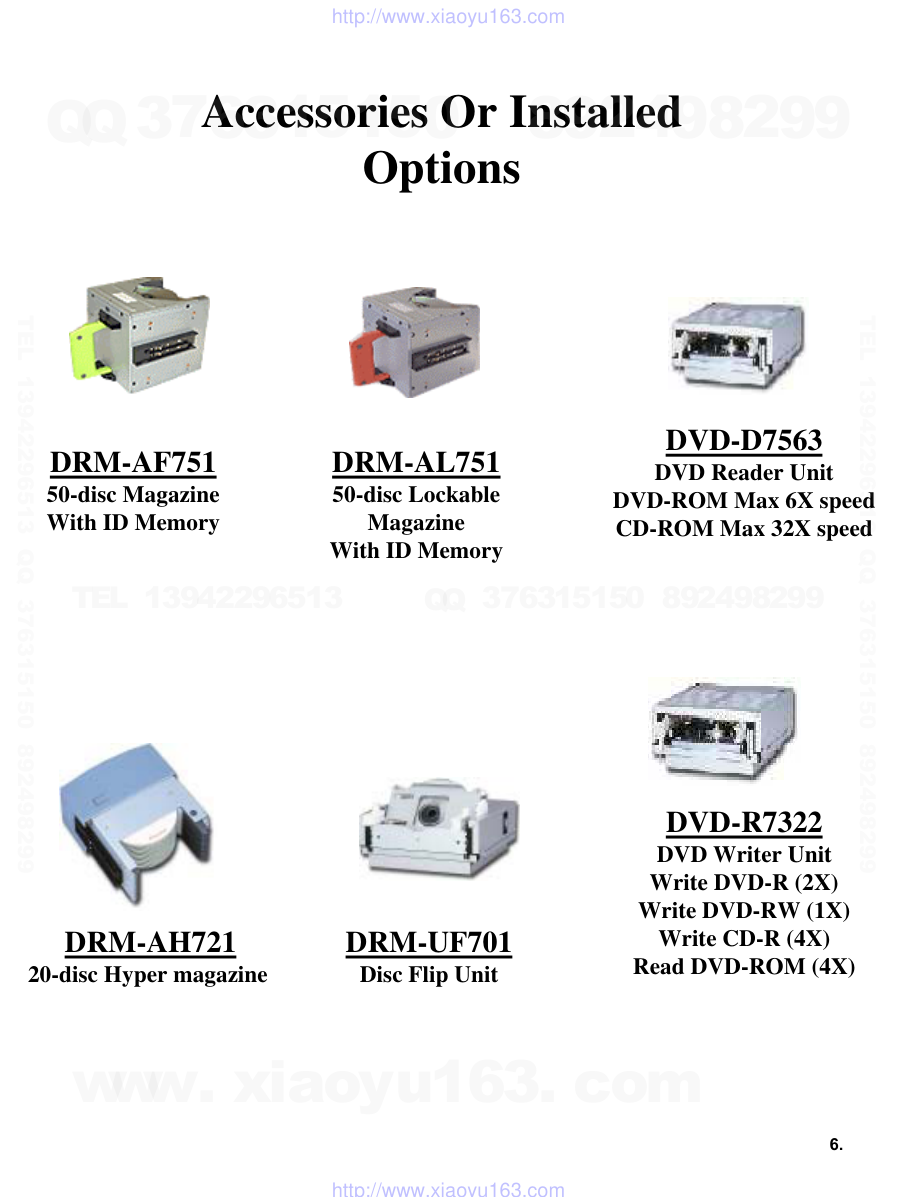)
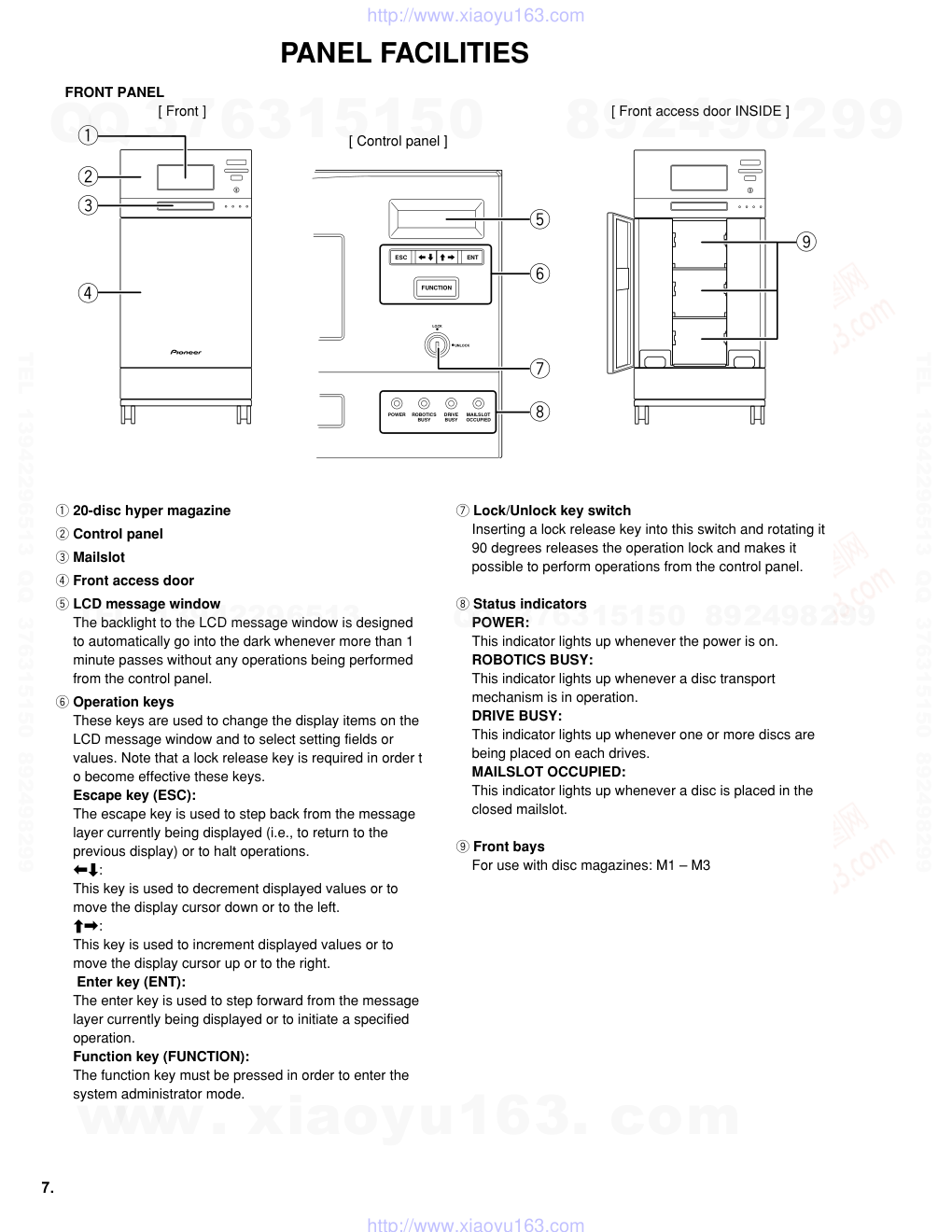)
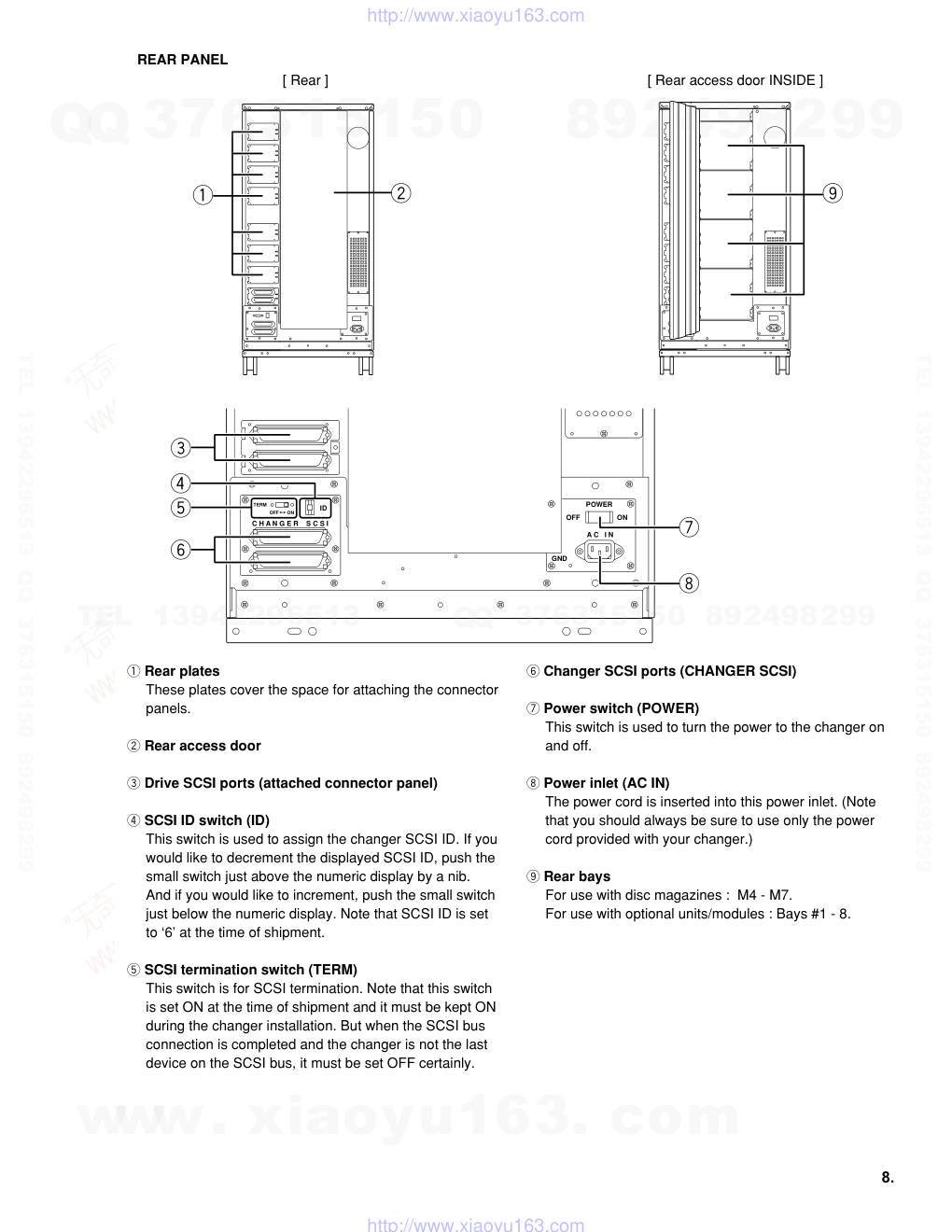)
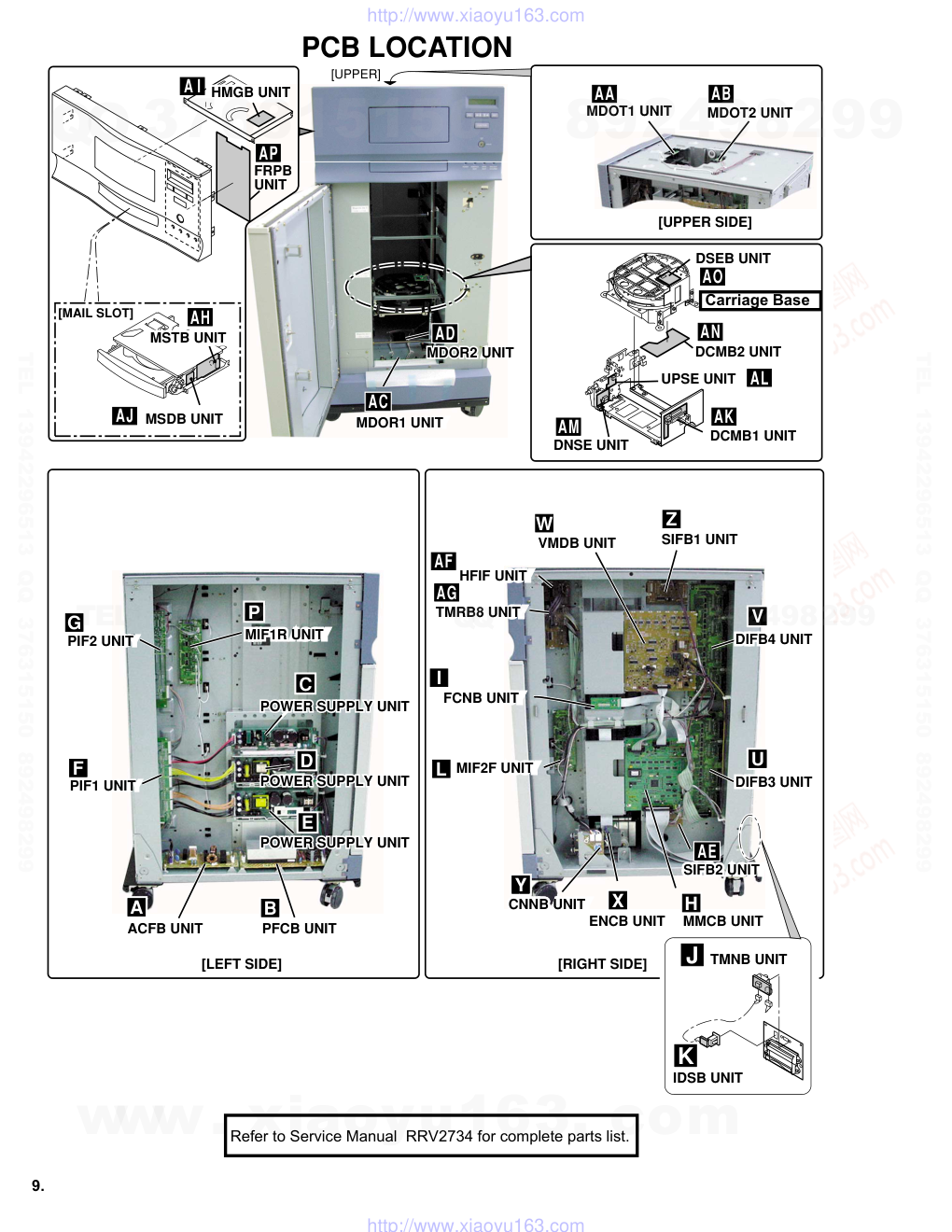)
Technical Training Field Repair Guide DVD/CD Library System DRM-3000 Multimedia & Web Training Department 545 Nolen Drive Suite 100 Southlake, Texas 76092 www. xiaoyu163. com QQ376315150 9 9 2 8 9 4 2 9 8 TEL 13942296513 9 9 2 8 9 4 2 9 8 0 5 1 5 1 3 6 7 3 Q Q TEL 13942296513 QQ 376315150 892498299 TEL 13942296513 QQ 376315150 892498299 http://www.xiaoyu163.com www. xiaoyu163. com QQ 376315150 9 9 2 8 9 4 2 9 8 TEL 13942296513 9 9 2 8 9 4 2 9 8 0 5 1 5 1 3 6 7 3 Q Q TEL 13942296513 QQ 376315150 892498299 TEL 13942296513 QQ 376315150 892498299 http://www.xiaoyu163.com Table Of Contents Safety Information……………3 Test Mode………….40~43 Specifications………………….4 Troubleshooting…...44~46 Media Storage Capacity………5 Error Codes………..46~51 Accessories and Options………6 Error-Log Codes…..52~59 Panel Facilities…………………7~8 Physical Addresses….60 PCB Locations…………………9 SCSI Sense Code……61 PCB Part Numbers……………10 Diagnosis Program..62~63 Power Supply Block Diagram…11~12 Circuit Board Descriptions……13~14 Overall Wiring Diagrams……..15~20 Disassembly…………………….21~24 Carriage Base Maintenance…..25~26 Cleaning………………………..27~28 Adjustments……………………29~37 System Administrator Mode….38~39 www. xiaoyu163. com QQ 376315150 9 9 2 8 9 4 2 9 8 TEL 13942296513 9 9 2 8 9 4 2 9 8 0 5 1 5 1 3 6 7 3 Q Q TEL 13942296513 QQ 376315150 892498299 TEL 13942296513 QQ 376315150 892498299 http://www.xiaoyu163.com SAFETY INFORMATION This manual is intended for qualified service technicians ; it is not meant for the casual do-it-yourselfer. Qualified technicians have the necessary test equipment and tools, and have been trained to properly and safely repair complex products such as those covered by this manual. Improperly performed repairs can adversely affect the safety and reliability of the product and may void the warranty. If you are not qualified to perform the repair of this product properly and safely, you should not risk trying to do so and refer the repair to a qualified service technician. WARNING This product contains lead in solder and certain electrical parts contain chemicals which are known to the state of California to cause cancer, birth defects or other reproductive harm. Health & Safety Code Section 25249.6 - Proposition 65 1. SAFETY PRECAUTIONS The following check should be performed for the continued protection of the customer and service technician. LEAKAGE CURRENT CHECK Measure leakage current to a known earth ground (water pipe, conduit, etc.) by connecting a leakage current tester such as Simpson Model 229-2 or equivalent between the earth ground and all exposed metal parts of the appliance (input/output terminals, screwheads, metal overlays, control shaft, etc.). Plug the AC line cord of the appliance directly into a 120V AC 60Hz outlet and turn the AC power switch on. Any current measured must not exceed 0.5mA. ANY MEASUREMENTS NOT WITHIN THE LIMITS OUTLINED ABOVE ARE INDICATIVE OF A POTENTIAL SHOCK HAZARD AND MUST BE CORRECTED BEFORE RETURNING THE APPLIANCE TO THE CUSTOMER. 2. PRODUCT SAFETY NOTICE Many electrical and mechanical parts in the appliance have special safety related characteristics. These are often not evident from visual inspection nor the protection afforded by them necessarily can be obtained by using replacement components rated for voltage, wattage, etc. Replacement parts which have these special safety characteristics are identified in this Service Manual. Electrical components having such features are identified by marking with a on the schematics and on the parts list in this Service Manual. The use of a substitute replacement component which does not have the same safety characteristics as the PIONEER recommended replacement one, shown in the parts list in this Service Manual, may create shock, fire, or other hazards. Product Safety is continuously under review and new instructions are issued from time to time. For the latest information, always consult the current PIONEER Service Manual. A subscription to, or additional copies of, PIONEER Service Manual may be obtained at a nominal charge from PIONEER. Leakage current tester Reading should not be above 3.5 mA Device under test Test all exposed metal surfaces Also test with plug reversed (Using AC adapter plug as required) Earth ground AC Leakage Test (FOR USA MODEL ONLY) www. xiaoyu163. com QQ 376315150 9 9 2 8 9 4 2 9 8 TEL 13942296513 9 9 2 8 9 4 2 9 8 0 5 1 5 1 3 6 7 3 Q Q TEL 13942296513 QQ 376315150 892498299 TEL 13942296513 QQ 376315150 892498299 http://www.xiaoyu163.com 3. SPECIFICATIONS [ 300 DISC CHANGER ] Description ............................................... 300 disc changer Power supply ............................. AC 100V-240V, 50/60 Hz Power consumption ................... Maximum of 3.3A (300 W) Weight of main unit (including placement fixtures) 60.6 kg (133 lb 10oz) External dimensions (including placement fixtures) 760 x 729 x 872 mm (W x D x H) 29-15/16 x 28-11/16 x 34-5/16in (W x D x H) Operating requirements * .......................... +5°C to +35°C Humidity * ....................... 5% to 85% (with no condensation) Storage requirements ................................ –40°C to +60°C * The figures for permissible operating temperature and humidity may change depending on the components loaded. For details, consult the operating instructions for each component used. Functional specifications Maximum number of discs ...................... 320 (12-cm discs) Maximum number of disc magazines 50-disc magazines ....................................................... 6 20-disc hyper magazine ................................................ 1 Maximum number of drives .............................................. 8 Items included 20-disc hyper magazine ................................................... 1 Changer/drive SCSI cable ................................................. 1 Power cord (for use in Canada and USA) ........................ 1 Power cord (for use in Japan) .......................................... 1 Base stabilizer ................................................................... 2 Screw for use in attaching Base stabilizer ........................ 6 Lock release key .............................................................. 2 Operations Instructions ..................................................... 1 ¶The external design of this product or any of the above specifications may be changed at any time without prior notification. SCSI connector specifications 1) Pin layout of SCSI connectors NOTES: ¶ Pin No. 12 to 14, 37 and 39 are not grounded. ¶ The connectors are of the shielded type. ¶ For details on the control commands, refer to the separate specifications manual. 2) Electrical specifications of SCSI GROUND GROUND GROUND GROUND GROUND GROUND GROUND GROUND GROUND GROUND GROUND NC NC NC GROUND GROUND GROUND GROUND GROUND GROUND GROUND GROUND GROUND GROUND GROUND 1 2 3 4 5 6 7 8 9 10 11 12 13 14 15 16 17 18 19 20 21 22 23 24 25 26 27 28 29 30 31 32 33 34 35 36 37 38 39 40 41 42 43 44 45 46 47 48 49 50 DB(0) -DB(1) -DB(2) -DB(3) -DB(4) -DB(5) -DB(6) -DB(7) -DB(P) GROUND GROUND NC TERMPWR NC GROUND -ATN GROUND -BSY -ACK -RST -MSG -SEL -C/D -REQ -I/O Signal name Pin No. Signal name Output characteristics Input characteristics The signals driven by SCSI equipment present the following output characteristics. True (LOW): VOL = 0.0 to 0.4 V DC IOL = 48 mA (0.5 V DC) max. False (HIGH): VOH = 2.5 to 5.25 V DC The signals driven by SCSI equipment present the following input characteristics. True (LOW): VOL = 0.0 to 0.4 V DC IOL = -0.4 mA (0.4 V DC) max. False (HIGH): VOH = 2.0 to 5.25 V DC NOTES: ¶ As the SCSI interface is of the single-ended type, it should be terminated on both ends of the cable . ¶ The maximum recommended length of an SCSI cable is 6 meters (20 feet) (including internal wiring). 1 ¡ ± + Base stabilizer ... x 2 (DNH2385) Lock release key ... x 2 (DXC1006) Power cord (for use in Canada and USA) ... x 1 (DDG1071) Power cord (for use in Japan) ... x 1 (DDG1047) Changer/drive SCSI cable ... x 1 (DDC1006) 20 disc hyper magazine ... x 1 [ Accessories ] This type of power cord is for use in America and Canada only. Do use this power cord in places other than America or Canada. This type of power cord is for use in Japan only. Do not use this power cord in a places other than Japan. Screw for use in attaching placement fixtures ............ x 6 Operating instructions ....... x 1 Warranty ........................... x 1 Service network sheet ...... x 1 www. xiaoyu163. com QQ 376315150 9 9 2 8 9 4 2 9 8 TEL 13942296513 9 9 2 8 9 4 2 9 8 0 5 1 5 1 3 6 7 3 Q Q TEL 13942296513 QQ 376315150 892498299 TEL 13942296513 QQ 376315150 892498299 http://www.xiaoyu163.com 4. DRM-3000 Media Storage Capacity CD (GB) DVD (TB) Double DVD (TB) Capacities Number of 50-disc Magazines Number OF Discs Number of Drives (when using flip unit) 8 (6) 3 170 111 0.80 1.60 6 (4) 4 220 143 1.03 2.07 4 (2) 5 270 176 1.27 2.54 2 6 320 208 1.50 3.01 Capacity values are calculated using DVD storage disc Single sided = 4.7GB. And CD-R media = 650MB. Flip Unit required for double sided media. Hyper Magazine increases storage by 20 discs. www. xiaoyu163. com QQ376315150 9 9 2 8 9 4 2 9 8 TEL 13942296513 9 9 2 8 9 4 2 9 8 0 5 1 5 1 3 6 7 3 Q Q TEL 13942296513 QQ 376315150 892498299 TEL 13942296513 QQ 376315150 892498299 http://www.xiaoyu163.com 5. Accessories Or Installed Options DVD-D7563 DVD Reader Unit DVD-ROM Max 6X speed CD-ROM Max 32X speed DRM-AF751 50-disc Magazine With ID Memory DRM-AL751 50-disc Lockable Magazine With ID Memory DVD-R7322 DVD Writer Unit Write DVD-R (2X) Write DVD-RW (1X) Write CD-R (4X) Read DVD-ROM (4X) DRM-AH721 20-disc Hyper magazine DRM-UF701 Disc Flip Unit www. xiaoyu163. com QQ376315150 9 9 2 8 9 4 2 9 8 TEL 13942296513 9 9 2 8 9 4 2 9 8 0 5 1 5 1 3 6 7 3 Q Q TEL 13942296513 QQ 376315150 892498299 TEL 13942296513 QQ 376315150 892498299 http://www.xiaoyu163.com 6. PANEL FACILITIES 9 1 2 3 4 ESC ENT FUNCTION LOCK POWER UNLOCK ROBOTICS BUSY DRIVE BUSY MAILSLOT OCCUPIED 5 6 7 8 [ Front ] [ Front access door INSIDE ] [ Control panel ] 1 20-disc hyper magazine 2 Control panel 3 Mailslot 4 Front access door 5 LCD message window The backlight to the LCD message window is designed to automatically go into the dark whenever more than 1 minute passes without any operations being performed from the control panel. 6 Operation keys These keys are used to change the display items on the LCD message window and to select setting fields or values. Note that a lock release key is required in order t o become effective these keys. Escape key (ESC): The escape key is used to step back from the message layer currently being displayed (i.e., to return to the previous display) or to halt operations. |«: This key is used to decrement displayed values or to move the display cursor down or to the left. »\: This key is used to increment displayed values or to move the display cursor up or to the right. Enter key (ENT): The enter key is used to step forward from the message layer currently being displayed or to initiate a specified operation. Function key (FUNCTION): The function key must be pressed in order to enter the system administrator mode. 7 Lock/Unlock key switch Inserting a lock release key into this switch and rotating it 90 degrees releases the operation lock and makes it possible to perform operations from the control panel. 8 Status indicators POWER: This indicator lights up whenever the power is on. ROBOTICS BUSY: This indicator lights up whenever a disc transport mechanism is in operation. DRIVE BUSY: This indicator lights up whenever one or more discs are being placed on each drives. MAILSLOT OCCUPIED: This indicator lights up whenever a disc is placed in the closed mailslot. 9 Front bays For use with disc magazines: M1 – M3 FRONT PANEL www. xiaoyu163. com QQ 376315150 9 9 2 8 9 4 2 9 8 TEL 13942296513 9 9 2 8 9 4 2 9 8 0 5 1 5 1 3 6 7 3 Q Q TEL 13942296513 QQ 376315150 892498299 TEL 13942296513 QQ 376315150 892498299 http://www.xiaoyu163.com 7. [ Rear access door INSIDE ] [ Rear ] 1 Rear plates These plates cover the space for attaching the connector panels. 2 Rear access door 3 Drive SCSI ports (attached connector panel) 4 SCSI ID switch (ID) This switch is used to assign the changer SCSI ID. If you would like to decrement the displayed SCSI ID, push the small switch just above the numeric display by a nib. And if you would like to increment, push the small switch just below the numeric display. Note that SCSI ID is set to ‘6’ at the time of shipment. 5 SCSI termination switch (TERM) This switch is for SCSI termination. Note that this switch is set ON at the time of shipment and it must be kept ON during the changer installation. But when the SCSI bus connection is completed and the changer is not the last device on the SCSI bus, it must be set OFF certainly. 6 Changer SCSI ports (CHANGER SCSI) 7 Power switch (POWER) This switch is used to turn the power to the changer on and off. 8 Power inlet (AC IN) The power cord is inserted into this power inlet. (Note that you should always be sure to use only the power cord provided with your changer.) 9 Rear bays For use with disc magazines : M4 - M7. For use with optional units/modules : Bays #1 - 8. TERM OFF ON ID C H A N G E R S C S I ON OFF GND POWER A C I N 7 8 3 6 5 4 1 2 9 REAR PANEL www. xiaoyu163. com QQ 376315150 9 9 2 8 9 4 2 9 8 TEL 13942296513 9 9 2 8 9 4 2 9 8 0 5 1 5 1 3 6 7 3 Q Q TEL 13942296513 QQ 376315150 892498299 TEL 13942296513 QQ 376315150 892498299 http://www.xiaoyu163.com 8. PCB LOCATION G T MDOT1 UNIT D D MDOT2 UNIT F W Z I L MIF1R ASSY A MIF1R UNIT P ACFB UNIT PFCB UNIT SIFB1 UNIT VMDB UNIT PIF2 ASSY PIF1 ASSY PIF2 UNIT PIF1 UNIT A B C C D E SIFB2 ASSY SIFB2 UNIT HFIF ASSY FCNB ASSY MIF2F ASSY HFIF UNIT FCNB UNIT MIF2F UNIT W U T DIFB4 ASSY DIFB3 ASSY MMCB ASSY CNNB ASSY CNNB ASSY U W V W A W B H Y DIFB4 UNIT DIFB3 UNIT MMCB UNIT IDSB UNIT TMNB UNIT CNNB ASSY CNNB UNIT [LEFT SIDE] [UPPER SIDE] [RIGHT SIDE] TMRB8 ASSY TMRB8 UNIT SIFB2 ASSY ENCB UNIT VX MDOR2 ASSY MDOR1 ASSY MDOR2 UNIT MDOR1 UNIT DCMB2 UNIT DSEB UNIT DCMB1 UNIT A K UPSE UNIT DNSE UNIT [UPPER] A H MSDB UNIT FRPB UNIT HMGB UNIT MSTB UNIT [MAIL SLOT] AF AJ A I AP AH AG AA AB AO AN AL AK AM AM AM AD AM AC J K POWER SUPPLY ASSY POWER SUPPLY UNIT POWER SUPPLY ASSY POWER SUPPLY UNIT POWER SUPPLY ASSY POWER SUPPLY UNIT AE AE www. xiaoyu163. com QQ 376315150 9 9 2 8 9 4 2 9 8 TEL 13942296513 9 9 2 8 9 4 2 9 8 0 5 1 5 1 3 6 7 3 Q Q TEL 13942296513 QQ 376315150 892498299 TEL 13942296513 QQ 376315150 892498299 http://www.xiaoyu163.com Refer to Service Manual RRV2734 for complete parts list. Carriage Base 9. PCB Part Numbers Location Description Part Number A ACFB DWR1316 AA MD0T1 DWX1989 AB MD0T2 DWX1988 AC MD0R1 DWX1992 AD MD0R2 DWX1991 AE SIFB2 DWX1990 AF HFIF DWX1983 AH MSTB DWX1984 AI HMGB DWX1986 AJ MSDB DWX1985 AK DCMB1 DWX1947 AL UPSE DWX1951 AM DNSE DWX1950 AN DCMB2 DWX1948 AO DSEB DWX1949 AP FRPB DWX1996 B PFCB DWR1315 C POWER SUPPLY 5V DWR1367 D POWER SUPPLY 12V DWR1368 E POWER SUPPLY 24V DWR1369 F PIF1 DWR1317 G PIF2 DRW1376 H MMCB DWX2268 I FCNB DWX1946 J TMNB DWX1994 K IDSB DWX1995 L MIF2F DWX1959 P MIF1R DWX1954 U DIFB3 DWX1956 V DIFB4 DWX1957 W VMDB DWX1981 X ENCB DWX1982 Y CNNB DWX1993 Z SIFB1 DWX2274 www. xiaoyu163. com QQ 376315150 9 9 2 8 9 4 2 9 8 TEL 13942296513 9 9 2 8 9 4 2 9 8 0 5 1 5 1 3 6 7 3 Q Q TEL 13942296513 QQ 376315150 892498299 TEL 13942296513 QQ 376315150 892498299 http://www.xiaoyu163.com Carriage Base Service Parts: Carriage Base Assy DXX2451 Chuck Assy DXX2348 10. BLOCK DIAGRAM POWER SUPPLY SIGNAL ROUTE 1 2 1 2 CN201 CN203 1 2 1 2 1 3 CN207 1 3 4 2 CN262 CN211 CN208 CN202 1 2 7 8 5 6 3 4 1 2 5 6 3 4 1 2 3 4 1 2 3 4 CN1 CN2 +5V V+5 POWER SUPPLY ASSY 1 2 CN209 1 2 CN1 1 - 6 6 5 4 3 2 1 1 2 3 4 6 5 4 3 2 1 CN2 +12V V+12 POWER SUPPLY ASSY 1 2 CN210 1 2 CN1 1 - 6 +5V GND5 1 - 6 +12V +12V +12V +12V GND12 +5V 1 - 6 CN2 CN251 CN277 CN267 CN951 CN252 CN254 +24v 1 - 7 1 - 6 CN3 CN255 GND24 GND24 V+5D GNDD +24v +24v CN263 CN271 CN279 +5V V+24 POWER SUPPLY ASSY Rear Bay #4 CN261 +5V GND5 GND5 GND GND GND5 GND12 GND12 GND12 2 1 +12v 7 8 5 6 3 4 1 2 1 2 +12V +12V PIF2 UNIT G PFCB UNIT B ACFB UNIT A C D E PIF1 UNIT F AC100 -240V 50/60Hz AC INLET 1 2 3 4 1 2 3 4 GND5 +12V GND12 +5V CN266 CN951 Rear Bay #3 1 2 3 4 1 2 3 4 GND5 +12V GND12 +5V CN265 CN951 Rear Bay #2 1 2 3 4 1 2 3 4 GND5 +12V GND12 +5V CN264 CN951 Rear Bay #1 GND12 GND24 1 - 7 1 - 6 CN3 CN253 GND12 GND12 GND5 GND5 AC(L) AC(N) AC(L) AC(N) AC(L) AC(N) AC(L) AC(N) AC(L) AC(N) 1 2 3 1 2 3 4 1 2 3 4 +5V GND5 +12V GND12 +5V CN275 CN951 CN279 Rear Bay #8 +5V 1 2 3 4 1 2 3 4 GND5 +12V GND12 +5V CN274 CN951 Rear Bay #7 1 2 3 4 1 2 3 4 GND5 +12V GND12 +5V CN273 CN951 Rear Bay #6 1 2 3 4 1 2 3 4 GND5 +12V GND12 +5V CN272 CN951 Rear Bay #5 V+12F V+12F V+5.1 V+12 IC272 GND POWER SW DC FAN MOTOR 8 4 3 7 9 2 8 10 V - V - AC AC V + V - V + V - V + V - V + PR AUX IOG IC201 www. xiaoyu163. com QQ 376315150 9 9 2 8 9 4 2 9 8 TEL 13942296513 9 9 2 8 9 4 2 9 8 0 5 1 5 1 3 6 7 3 Q Q TEL 13942296513 QQ 376315150 892498299 TEL 13942296513 QQ 376315150 892498299 http://www.xiaoyu163.com 11. 5 6 3 4 1 3 CN102 CN105 V+5D GNDD GNDD GND12 GND15 GNDD CN101 CN107 2 1 +5V V+5D V+5D V+5D IC143 IC144 +12v MMCB UNIT HMIF UNIT HMGB UNIT HYPER SLOT MAIL SLOT MSTB UNIT FCNB UNIT H MIF2F UNIT L = & 7 8 CN117 1 9 ~ ! CN106 1 2 CN112 3 - 6 @ - % CN116 ~ - @ + - ™ CN872 V+5D VSWD15 VSWD12 IC145 V+12 IC131 CN104 1 2 V+5D GNDD GNDD V+5D V+5D IC141 GND12 CN103 1 2 V+5D V+5D V+12 VSWD12 GNDD GNDD V+5D IC142 CN421 1 2 V+5D GNDD GNDD GND12 GND12 ∞ ¢ £ ™ 2 1 CN108 V+5D GNDD GND12 GND12 GNDD GNDD V+5D VSWD12 GNDD MIF1R UNIT P R I V+5D CN626 1 2 V+5D GNDD GNDD GNDD V+5D V+5 CN810 6 7 V+5 GNDD 6 7 V+5 GNDD GNDD 6 7 GNDD V+5D V+5 V+5D V+12 V+12 V+5 V+12 V+5D V+12 CN803 CN802 CN805 6 7 V+5 V+5 GNDD GND5 GND12 GND5 GND12 CN602 V+5D V+5D 1 4 GND24 CN606 V+12 VSWD15 4 3 2 1 GND12 VMDB UNIT W V+5D VSWD15 VSWD12 GNDD GND12 GND15 ENCB UNIT X V+5D CN613 1 4 GNDD DNSE UNIT V+5D J841 CN875 4 3 4 3 GNDD UPSE UNIT Carriage Base Section V+5D V+5D V+12 V+5 V+5 V+5 V+5 V+5D V+5D V+5D V+5D V+5D V+5D V+5D V+5D J831 CN874 2 3 2 3 GNDD FRPB UNIT Z SIFB1 UNIT DCMB1 UNIT SIFB2 UNIT DCMB2 UNIT 3 5 7 9 CN871 # % = ! CN876 DSEB UNIT V+5D CN873 J851 2 3 2 3 GNDD GNDD GNDD GNDD GNDD GNDD GNDD 1 2 3 4 CN814 V+12 V+12 V+5 GND5 GND12 V+12 GNDD GNDD CN860 1 2 MDOR1 UNIT MDOR2 UNIT V+5 CN861 1 2 GND5 GND5 GND12 V+5 GND5 1 2 3 5 $ % CN801 1 2 3 5 $ % ^ & ~ ! 2 CN601 1 @ # $ % ^ & ^ & V+5D V+5 1 3 V+5 1 3 GNDD CN807 CN809 V+5 CN111 2 1 1 2 CN856 1 2 3 4 CN701 U DIFB3 UNIT V+5D V+5D VSWD12 VSWD12 GND12 GND12 GNDD GNDD V+5D 1 2 ™ £ ¢ ∞ CN301 1 2 ™ £ ¢ ∞ CN306 V DIFB4 UNIT V+5D VSWD12 GND12 GNDD CN501 1 2 ™ £ ¢ ∞ V+12 GND12 GNDD V+12 1 2 CN851 CN868 1 2 CN869 1 2 IC854 A F A H MSDB UNIT A J A I A K A N A O A M A L A E A D A C VSWD12 IC621 IC619 IC620 V-12 IC617 IC615 IC616 GND12 IC130 V+5D VSWD12 VSWD12 VSWD12 VSWD12 GND12 GNDD V+5D VSWD12 GND12 VSWD12 GND12 GNDD CN302 CN901 ! @ $ % ^ & Rear Bay #1 ! @ $ % ^ & V+5D VSWD12 GND12 VSWD12 GND12 GNDD CN303 CN901 ! @ $ % ^ & Rear Bay #2 ! @ $ % ^ & V+5D VSWD12 GND12 VSWD12 GND12 GNDD CN304 CN901 ! @ $ % ^ & Rear Bay #3 ! @ $ % ^ & V+5D VSWD12 GND12 VSWD12 GND12 GNDD CN305 CN901 ! @ $ % ^ & Rear Bay #4 ! @ $ % ^ & V+5D GND12 GNDD V+5D GND12 GNDD V+5D GND12 GNDD V+5D VSWD12 VSWD12 VSWD12 VSWD12 GND12 GNDD V+5D VSWD12 GND12 VSWD12 GND12 GNDD CN502 CN901 ! @ $ % ^ & Rear Bay #5 ! @ $ % ^ & V+5D VSWD12 GND12 VSWD12 GND12 GNDD CN503 CN901 ! @ $ % ^ & Rear Bay #6 ! @ $ % ^ & V+5D VSWD12 GND12 VSWD12 GND12 GNDD CN504 CN901 ! @ $ % ^ & Rear Bay #7 ! @ $ % ^ & V+5D VSWD12 GND12 VSWD12 GND12 GNDD CN505 CN901 ! @ $ % ^ & Rear Bay #8 ! @ $ % ^ & V+5D GND12 GNDD V+5D GND12 GNDD V+5D GND12 GNDD ~ ! 1 2 @ # $ % ^ & www. xiaoyu163. com QQ 376315150 9 9 2 8 9 4 2 9 8 TEL 13942296513 9 9 2 8 9 4 2 9 8 0 5 1 5 1 3 6 7 3 Q Q TEL 13942296513 QQ 376315150 892498299 TEL 13942296513 QQ 376315150 892498299 http://www.xiaoyu163.com +15 Volt Regulator -12 DC to DC Converter +5 Volt Regulator +5 +12 +24 +15 12. Circuit Board Descriptions (A) ACFB unit. Connects to the AC line cord input and power switch. Contains a AC line filter and main 6.3 amp 250 volt fuse. (B) PFCB unit. Power Factor Improvement Module. Receives AC input from ACFB unit and provides the AC supply for the three power supplies. (C), (D) and (E). (C) +5 Volt Power Supply. Supply for PCB units and bays. (D) +12 Volt Power Supply. Supply for PCB units and bays. (E) +24 Volt Power Supply. Supply for VMDB unit (Vertical Motor Drive board). (F) PIF1 unit. Power interface assembly for rear bays 1~4. (G) PIF2 unit. Power interface assembly for rear bays 5~8, DC fan power connector and fan FG circuit. (H) MMCB unit. Main Microprocessor Circuit Board. This unit contains the main CPU, SCSI interface, Flash Rom and integrated circuit protectors for +5 and +12 volt supplies. (I) FCNB unit. Interconnect from MMCB to DCMB1 units. Contains the up/down interrupter LED’s for vertical drive motor stop position. (Fixed). (J) TMNB unit. Contains the SCSI termination switch and provides the feed through from the MMCB to the IDSB units. (K) IDSB unit. SCSI ID selector for the changer. (L) MIF2F unit. Touch Memory Interface Assembly. Connects from touch memory units (M, N and O) to the MMCB unit. (See service manual for locations of magazine touch memory units). (P) MIF1R unit. Touch Memory Interface Assembly. Connects from touch memory units (Q, R, S and T) to MMCB unit. (U) DIFB3 unit. Rear Bay 1~4 SCSI Terminal Interface. (V) DIFB4 unit. Rear Bay 5~8 SCSI Terminal Interface. (W) VMDB unit. Vertical Motor Drive Board. Contains the vertical motor drive circuit, door switches and front/rear door plunger drivers. www. xiaoyu163. com QQ 376315150 9 9 2 8 9 4 2 9 8 TEL 13942296513 9 9 2 8 9 4 2 9 8 0 5 1 5 1 3 6 7 3 Q Q TEL 13942296513 QQ 376315150 892498299 TEL 13942296513 QQ 376315150 892498299 http://www.xiaoyu163.com 13. (X) ENCB unit. Up/Down rotation detector. Connects to the VMDB unit. (Y) CNNB unit. Vertical Motor Connector Assembly. (Z) SIFB1 unit. Disc Detect Sensor Adjustment Board. (AA) MDOT1 unit. Front Disc Sensor LED Board. (AB) MDOT2 unit. Rear Disc Sensor LED Board. (AC) MDOR1 unit. Front Disc Sensor (photo coupler). (AD) MDOR2 unit. Rear Disc Sensor (photo coupler). (AE) SIFB2 unit. Sensor interface board. Connects to disc sensors, door switches and the MMCB unit. (AF) HMIF unit. Hyper Magazine Interface Board. Signal interface to and from the MMCB unit. (AH) MSTB unit. Mail slot tray motor connector, tray open/close switch and rotation encoder connector. (AI) HMGB unit. Hyper magazine loading motor connector, sensor release switch and load/unload switch connector. (AJ) MSDB unit. Mail Slot Rotary Encoder. (AK) DCMB1 unit. Carriage Base Main Interconnect Assembly. (AL) UPSE unit. Carriage base up sensor assembly. (AM) DNSE unit. Carriage base down sensor assembly. (AN) DCNB2 unit. Carriage base loading motor connector and disc detect LED assembly. (AO) DSEB unit. Carriage base disc detector adjustment assembly. (AP) FRPB unit. Front Panel PCB Board. Function LED’s, function button assembly, LCD module connector and key lock interface. www. xiaoyu163. com QQ 376315150 9 9 2 8 9 4 2 9 8 TEL 13942296513 9 9 2 8 9 4 2 9 8 0 5 1 5 1 3 6 7 3 Q Q TEL 13942296513 QQ 376315150 892498299 TEL 13942296513 QQ 376315150 892498299 http://www.xiaoyu163.com 14. OVERALL WIRING DIAGRAM (1/3) ACFB UNIT (DWR1316) A PIF1 UNIT (DWR1317) Rear Bay #4 Rear Bay #5 Rear Bay #6 Rear Bay #7 Rear Bay #8 Rear Bay #3 Rear Bay #2 Rear Bay #1 POWER SW DSA1027 DC FAN MOTOR DXM1183 POWER CORD DDG1071 (for North American) DDG1047 (for Japan) 3P INLET ASSY DKN1194 F PIF2 UNIT (DWR1376) G PFCB UNIT (DWR1315) B POWER SUPPLY ASSY (DWR1367) C POWER SUPPLY ASSY (DWR1368) D POWER SUPPLY ASSY (DWR1369) SWITCHING REGULATOR E www. xiaoyu163. com QQ 376315150 9 9 2 8 9 4 2 9 8 TEL 13942296513 9 9 2 8 9 4 2 9 8 0 5 1 5 1 3 6 7 3 Q Q TEL 13942296513 QQ 376315150 892498299 TEL 13942296513 QQ 376315150 892498299 http://www.xiaoyu163.com 15. +5v +12v +24v MMCB UNIT (DWX2268) TMNB UNIT (DWX1994) J IDSB UNIT (DWX1995) K A B C D E H 1/3- (1/3) (1/3) (1/3) (1/3) (2/3) (2/3) (3/3) H 3/3 H To CHANGER SCSI TERMINAL www. xiaoyu163. com QQ 376315150 9 9 2 8 9 4 2 9 8 TEL 13942296513 9 9 2 8 9 4 2 9 8 0 5 1 5 1 3 6 7 3 Q Q TEL 13942296513 QQ 376315150 892498299 TEL 13942296513 QQ 376315150 892498299 http://www.xiaoyu163.com 16. OVERALL WIRING DIAGRAM (2/3) MIF2F UNIT (DWX1959) Front Side Magazine 3 Rear Side L MIF1R UNIT (DWX1954) P TMRB1 UNIT (DWX1966) M TMRB2 UNIT (DWX1967) N TMRB3 UNIT (DWX1968) O TMRB4 UNIT (DWX1969) Q TMRB5 UNIT (DWX1970) R TMRB6 UNIT (DWX1971) S TMRB7 UNIT (DWX1972) T Magazine 2 Magazine 1 Magazine 4 Magazine 5 Magazine 6 Magazine 7 A B C E www. xiaoyu163. com QQ 376315150 9 9 2 8 9 4 2 9 8 TEL 13942296513 9 9 2 8 9 4 2 9 8 0 5 1 5 1 3 6 7 3 Q Q TEL 13942296513 QQ 376315150 892498299 TEL 13942296513 QQ 376315150 892498299 http://www.xiaoyu163.com 17. DIFB3 UNIT (DWX1956) U DIFB4 UNIT (DWX1957) V Rear Bay #5 Rear Bay #2 Rear Bay #3 Rear Bay #4 Rear Bay #7 Rear Bay #8 Rear Bay #1 Rear Bay #6 www. xiaoyu163. com QQ 376315150 9 9 2 8 9 4 2 9 8 TEL 13942296513 9 9 2 8 9 4 2 9 8 0 5 1 5 1 3 6 7 3 Q Q TEL 13942296513 QQ 376315150 892498299 TEL 13942296513 QQ 376315150 892498299 http://www.xiaoyu163.com 18. OVERALL WIRING DIAGRAM (3/3) DCMB1 UNIT (DWX1947) FCNB UNIT (DWX1946) DNSE UNIT (DWX1950) CARRIAGE ASSY-S (DXX2451) MAIL SLOT SECTION HIPER MAGAZINE SECTION I AM AK DCMB2 UNIT (DWX1948) AN MSDB UNIT (DWX1985) AJ TMRB8 UNIT (DWX1973) AG MSTB UNIT (DWX1984) AH HMIF UNIT (DWX1983) AF HMGB UNIT (DWX1986) AI UPSE UNIT (DWX1951) AL DSEB UNIT (DWX1949) LOADING MOTOR ASSY-S DXX2522 DISC DET. SENSOR ADJ. SHIPPING SW (R) DSK1007 FOR ADJ TRAY O/C DET. SW DSK1003 TRAY MOTOR PXM1002 RELEASE SENSOR SW VSH1017 LOAD END/ UNLOAD SW DSK1003 HP LOADING MOTOR ASSY-S DXX2452 SHIPPING SW (L) DSK1007 AO (2/3) (2/3) (2/3) (2/3) (2/3) www. xiaoyu163. com QQ 376315150 9 9 2 8 9 4 2 9 8 TEL 13942296513 9 9 2 8 9 4 2 9 8 0 5 1 5 1 3 6 7 3 Q Q TEL 13942296513 QQ 376315150 892498299 TEL 13942296513 QQ 376315150 892498299 http://www.xiaoyu163.com 19. Z FRPB UNIT (DWX1996) LCD MODULE (DWG1507) AP SIFB2 UNIT (DWX1990) AE SIFB1 UNIT (DWX2274) Y CNNB UNIT (DWX1993) X ENCB UNIT (DWX1982) FERRITE CLAMP DTH1177 DOOR SW F DSK1007 PLUNGER F DXP1044 PLUNGER R DXP1044 DOOR SW R DSK1007 MDOR2 UNIT (DWX1991) AD MDOR1 UNIT (DWX1992) AC MDOT2 UNIT (DWX1988) AB MDOT1 UNIT (DWX1989) AA W 1/3- W 3/3 VMDB UNIT (DWX1981) W D LOCK/UNLOCK KEY SW DXC1005 WHT GRY DISC DET. SENSOR ADJ DISC DET. SENSOR ADJ VD MOTOR DXM1086 DISC DET. SENSOR ADJ FOR FACTORY ADJ DISC DET. SENSOR ADJ (2/3) (2/3) (1/3) MMCB UNIT (DWX2268) H 1/3- H 3/3 H UP/DOWN SPEED ADJ VR601 LCD POWER SUPPLY ADJ VR701 www. xiaoyu163. com QQ 376315150 9 9 2 8 9 4 2 9 8 TEL 13942296513 9 9 2 8 9 4 2 9 8 0 5 1 5 1 3 6 7 3 Q Q TEL 13942296513 QQ 376315150 892498299 TEL 13942296513 QQ 376315150 892498299 http://www.xiaoyu163.com 20. DISASSEMBLY 2 ×2 1 ×2 1 ×2 1 25 mm 30 mm 1 Remove the eight screws. 2 Note: Remove the side panel (ML) with the same way. Side Panel (M) Side Panel (M) Hook Side Panel (ML) 1 Lift the link plate assy. 2 Open the front door. 1 Insert a thin plate, such as a square, through the gap between the front door and the body, horizontally about 30 mm, and move the thin plate upward until it reaches the plate stopper. 2 Push up the plate stopper until it unlatches. 3 The front door can be opened manually. 1 2 1 ×2 1 2 3 Link Plate Assy Side Panel Remove the side panel (M) and (ML) after sliding to the sideways. Front Door Opening the Front Door Manually (1) Front Door Front Door Opening the Front Door Manually (2) Square Plate Stopper www. xiaoyu163. com QQ 376315150 9 9 2 8 9 4 2 9 8 TEL 13942296513 9 9 2 8 9 4 2 9 8 0 5 1 5 1 3 6 7 3 Q Q TEL 13942296513 QQ 376315150 892498299 TEL 13942296513 QQ 376315150 892498299 http://www.xiaoyu163.com 21. Rear Door D Belt Spring VD Motor Fixing Plate CNNB UNIT VD Motor 1 Insert a thin rod, such as a small-diameter screwdriver, diagonally down approx. 50 mm through the hole at the lower side of the rear door. 2 Move it to the direction indicated by the arrow. 3 Open the rear door. 1 2 3 Note: When reattaching the VD motor fixing plate, turn the four screws (2) until the tensions of the D belt spring and the S3M belt (3) are balanced. 2 1 3 3 3 3 ×2 Slide the screws (1) toward A and tighten. Put the S2M belt. Attach the VD motor with two screws (PMB30P060FMC) and a motor-sleeve screw (AMZ30P080FMC). Run these screws in but don't tighten them yet. 2 3 1 1 1 A (AMZ30P080FMC) (PMB30P060FMC) x2 VD Motor Motor-sleeve S2M Belt 2 2 2 Rear Door Thin rod, such as a small- diameter screwdriver Removing the VD Motor Fixing Plate Remove the side panel (M), located at right viewed from the front. Remove the four screws. Remove the D belt spring, S3M belt and the two connectors. Attaching the VD Motor S3M Belt 3 3 D Belt Spring www. xiaoyu163. com QQ 376315150 9 9 2 8 9 4 2 9 8 TEL 13942296513 9 9 2 8 9 4 2 9 8 0 5 1 5 1 3 6 7 3 Q Q TEL 13942296513 QQ 376315150 892498299 TEL 13942296513 QQ 376315150 892498299 http://www.xiaoyu163.com 22. Drive Unit PL Lock Lever -1 1 1 ×3 1 2 ×2 1 4 ×2 PL Lock Lever Drive Unit 2 Release the PL lock lever. 3 Remove the drive unit. 2 4 3 1 Remove the four screw. 2 3 4 Remove the PL upper cover. PL Upper Cover PL Upper Cover Drive Unit (Option) Remove three connectors. Reference: The reader drive can be installed in any slot. (You can install as many optional reader drives as there are slots available.) Removing the PL Upper Cover of the Drive Unit The PL upper cover is fixed with claws at the front and with screws at the rear. To remove the PL upper cover, proceed as follows. Failure to do so may damage the claws. While pressing the PL lock lever toward RELEASE, slide the PL upper cover backward. (It will stop after sliding approx. 1 cm backward.) Press and bend the front part of the PL upper cover from the left and right sides to unhook the claws, then lift up the cover. (Do NOT try to lift up the cover forcibly with the claws unhooked. This may damage the claws and make it impossible to reattach the cover.) Claw Claw • When reattaching the cover, reverse the above procedures. (Place the cover approx. 1 cm backward and hook the claws, then slide the cover forward.) • Observe the driver unit from the rear to check that the claws are firmly engaged. -2 2 -2 2 www. xiaoyu163. com QQ 376315150 9 9 2 8 9 4 2 9 8 TEL 13942296513 9 9 2 8 9 4 2 9 8 0 5 1 5 1 3 6 7 3 Q Q TEL 13942296513 QQ 376315150 892498299 TEL 13942296513 QQ 376315150 892498299 http://www.xiaoyu163.com 23. 1 Open the front door. 2 Remove the side panel (M), located at right viewed from the front. 3 Rotate the pulley with your fingers clockwise to move the carriage base downward, and counterclockwise to move it upward. Carriage base upward Carriage base downward Caution: If the front door switch is set to ON while the power is on, the motor shaft will start rotating. 1 Open the front and rear doors. Turn off the power. 2 Move the carriage base down until it touches the under chassis by manually rotating the shaft of the elevator motor. Refer to "6.1 Mechanism adjustment" and "6.2 Adjustment for mechanical operations". 4 Caution: If the carriage base does not touch the under chassis, the table of the carriage base will be deformed. 5 2 ×4 4 Moving the Carriage Base Up and Down Manually For Shipping Stopper Screw of the Carriage Base For safety, when moving the unit, fix the carriage base by the shipping stopper screws. Removing the Carriage Base Carriage base Carriage base Remove the four screws and remove the carriage base. 3 Remove the Flexible flat cable (F.F.C ) Reattaching the Carriage Base Reattach the carriage base with the four screws with the table of the carriage base touching the under chassis. Caution: Be sure to proceed with this step with the carriage base touching the under chassis. Otherwise, the table of the carriage base will be deformed. Entering Adjustment Mode Pulley www. xiaoyu163. com QQ 376315150 9 9 2 8 9 4 2 9 8 TEL 13942296513 9 9 2 8 9 4 2 9 8 0 5 1 5 1 3 6 7 3 Q Q TEL 13942296513 QQ 376315150 892498299 TEL 13942296513 QQ 376315150 892498299 http://www.xiaoyu163.com 24. Maintenance of the Carriage Base (1) Removing the Chuck Assy 1. Turn off the power. 2. Slide the chuck toward you by rotating the loading motor. 3. Lifting up the upper plate, pull the chuck assy from the shaft of the planetary arm. (2) Removing the Outer table 1. Remove the carriage base. (Refer to the section "Removing the Carriage Base". 2. Remove two fixing screws 1 and remove the sensor stay. Note : Make sure not to damage the wire. Also, be sure to remember the layout of the wire before removing. 3. Unlock the lock plate by sliding the plate with its side lifted. 4. Grip the chuck assy and the upper plate together so that the chuck assy will not move, and pull them out toward you. Note: Pull out the chuck assy and the upper plate slowly straight toward you so that the steel ball will not fall. After pulling them out, remove the steel ball. Upper Plate Chuck Assy Fig. 1 Fig. 2 1 Sensor Stay Lock Plate Fig. 3 Chuck Assy Upper Plate Fig. 4 www. xiaoyu163. com QQ 376315150 9 9 2 8 9 4 2 9 8 TEL 13942296513 9 9 2 8 9 4 2 9 8 0 5 1 5 1 3 6 7 3 Q Q TEL 13942296513 QQ 376315150 892498299 TEL 13942296513 QQ 376315150 892498299 http://www.xiaoyu163.com 25. (3) Attaching the Inner Table Assy 1. Mount the inner table assy so that the tip of the planetary arm assy is centered on the cutout of the outer table. Note: Make sure that the inner table assy is not mounted on the flange of the outer table. (4) Mounting the Outer table 1. Align the largest, key-shaped axis of the H cam gear of the carriage base and two SW arms C with the marks. 2. Turn the inner table of the outer table completely counterclockwise and keep it in that position. Note: Grip the chuck assy and the upper plate firmly so that the inner table will not return to its original position under its spring tension. 3. Insert the steel ball into the slot of the outer table. 4. Align the key-shaped slot of the inner table with the key- shaped axis of the H cam gear, and mount the outer table. Note: While mounting the inner table, press it on so that the inner table will not pop up from the outer table. 5. Slide the lock plate, and lock it. Note: Check that the lock plate is firmly locked by lifting the outer table. 6. Rotate the outer table one turn by rotating the loading motor. If the SW C arms are not seated in the cam grooves, the rotation will be locked midway. In this case, remove the swing-full assy and repeat steps 5 through 7. 7. Lay out the wire of the sensor stay and screw on the sensor stay. (5) Attaching the SW Arms 1. Attach the SW arms as indicated in Fig. 7. Note: There are three SW arms, labeled A, B and C. Outer Table (cutout) Planetary Arm Assy Planet Gear Fig. 5 marks Key-shaped axis of the H Cam gear (larged) SW Arms C marks Fig. 6 Loading Motor Assy Flexible cord SW Arm B (to inner cam groove) SW Arm B (to outer cam groove) H Cam Gear DCMB Unit SW Arm A (to outer cam groove) SW Arm C SW Arm C Fig. 7 www. xiaoyu163. com QQ 376315150 9 9 2 8 9 4 2 9 8 TEL 13942296513 9 9 2 8 9 4 2 9 8 0 5 1 5 1 3 6 7 3 Q Q TEL 13942296513 QQ 376315150 892498299 TEL 13942296513 QQ 376315150 892498299 http://www.xiaoyu163.com 26. INFORMATION ON MAINTENANCE 1. Open the door. Manually rotate the Loading Motor located at the lower part of the carriage base until the chuck comes to the front-panel side. 2. Turn the unit OFF. 3. Remove dust and dirt around the D-Guides for loading discs and the Chuck Guide on the carriage base. 7 Cleaning the chuck on the carriage base 7 Cleaning the Touch block of the Touch Memory • Fan Clean the fan before shipping. For cleaning, the following tool is required: • Cleaning paper GED-008 [ NOTES ON SERVICING ] 7 Cleaning the parts • Clean the Touch block of the Touch Memory. 7 Cleaning the Mailslot tray block • Eject the Mailslot tray block in Test mode and clean it. www. xiaoyu163. com QQ 376315150 9 9 2 8 9 4 2 9 8 TEL 13942296513 9 9 2 8 9 4 2 9 8 0 5 1 5 1 3 6 7 3 Q Q TEL 13942296513 QQ 376315150 892498299 TEL 13942296513 QQ 376315150 892498299 http://www.xiaoyu163.com 27. Raise the Outer Table as shown in the photo, and apply grease (GYA1001) around the steel ball, taking care not to overflow. Outer Table 7 Lubricating the carriage base • Lubricating the outer table 7 Lubricating the Planet Arm Assy • Rotate the Loading Motor manually until the D-Guides and the chuck come out sufficiently enough lubrication at the rear side. Care must be taken so that they do not fully protrude. Apply grease (GYA1001) to the oval-shaped holes (inside the circles in the photo) on the Planet Arm Assy. www. xiaoyu163. com QQ 376315150 9 9 2 8 9 4 2 9 8 TEL 13942296513 9 9 2 8 9 4 2 9 8 0 5 1 5 1 3 6 7 3 Q Q TEL 13942296513 QQ 376315150 892498299 TEL 13942296513 QQ 376315150 892498299 http://www.xiaoyu163.com 28. ADJUSTMENTS MECHANISM ADJUSTMENT Tools for Adjustment Preparations for Adjustment Adjustment Methods a : Phillips screwdriver (nominal No. 2 for M3 cross-recessed head machine screws) b : Phillips screwdriver (nominal No. 3 for M2.6 cross-recessed head machine screws) c : Flat-head screwdriver (nominal 5.5 × 75; for M2.6 slotted head machine screws) d : Hexagonal wrench (nominal 2.5 for M3 hexagon socket head cap screws) e : Hexagonal wrench (nominal 2 for M2.6 hexagon socket set screws) f : Door key g : Screw-fixing adhesive [Screw-fixing adhesive #300UB: ZBA-300UB] h : Adjustment disc [GGF1287] i : Adjustment filter [GGF1287] j : Flat-head screwdriver for volume adjustments (2.4mm, non-conducting type or an equivalent) k : Adhesive (Arontite R: ZBA-UR) l : Magazine for 50 discs (DRM-AF751)[GGF1435] Indications a to l at the end of paragraphs in the following indicate the tools to be used in the respective steps. • For adjustments of the mechanical operations (1) Remove the side panel (right side) and top panel. a (2) Open the front door and pull out the magazines. f Caution: Be careful when performing this step, because this unit operates at a high speed. ∗ As adjustments are to be performed with visual observation, set the unit in a well-lit place, such as under a fluorescent lamp. ∗ Note that the manual elevating operation mode of the Test mode. (Diag → Robotics → Individually) activates even when the D guides have been protruded. D guide ∗ Sufficient care must be taken as the chuck block is protruded if you rotate the turntable clockwise in manual loading operation of the Test mode (Diag → Robotics → Individually). It can cause damage if protruded in a location other than the disc rack and player. Chuck block • For sensitivity adjustment of the carriage base disc sensor (1) Remove the side panel (right side) and the top panel. a • For sensitivity adjustment of the magazine disc out-of-position sensor (1) Remove the side panel (right side) and the top panel. a (2) Open the front door and pull out the under magazine. f • The figures in brackets, such as [001], in the following represent the position of the carriage base displayed in the lower row of the mode indicator when you move it up or down operation mode. • To move the carriage base up or down by hand, remove the side panel (right side) and turn the pulley or the belt of the vertical drive motor counterclockwise for upward movement, and clockwise for downward movement. Refer to "Moving the carriage base up or down manually " of IN DISASSEMBLY. • How to enter Test Mode See TEST MODE." www. xiaoyu163. com QQ 376315150 9 9 2 8 9 4 2 9 8 TEL 13942296513 9 9 2 8 9 4 2 9 8 0 5 1 5 1 3 6 7 3 Q Q TEL 13942296513 QQ 376315150 892498299 TEL 13942296513 QQ 376315150 892498299 http://www.xiaoyu163.com 29. ADJUSTMENT FOR MECHANICAL OPERATIONS Height Adjustment of the D Guides L and R Right and Left Adjustment of the Carriage Base • Purpose : To adjust the top height of the D guides with respect to the reference surface of the carriage base. • Method : Turn the D guide adjustment screw (DG height pin) on the carriage base. • Contents : Adjust the top heights of the D guides L and R on the carriage base. Adjust the upper surface of the D guides to 31 ± 0.2 mm higher than the reference surface of the carriage base. • Preparation : Press the Door SW to cancel the operation restriction. Enter Manual elevating operation mode of the Test mode (Diag → Robotics → Individually). • Adjustment point: DG height pin • Left Side (1) Move the carriage base to a position (around [75] to [100] ) which permits it to be seen from the front and the loading motor to be rotated. (2) Rotate the turntable counterclockwise in Manual operation mode (Test → Diag → Robotics → Individually). Caution: Do not turn it clockwise to avoid damage. (3) Stop the rotation when the turntable has been turned about 70 degrees from the front. (4) Using a measuring device, confirm that the distance between the upper surface of the carriage base and the upper surface of the D guide is 31 mm. If not, adjust the D guide adjustment screw. c (5) Lock the screws when the adjustment is completed. k • Right side (1) As with the left side adjustment, rotate the turntable counterclockwise and stop it when it has been rotated about 290 degrees from the front. (2) The subsequent procedures are the same as for the left side adjustment. DG height pin Carriage base Carriage base Carriage base DG height pin Reference surface Reference surface D guide L D guide R 31 ± 0.2 mm 31 ± 0.2 mm Fig. 1 Height adjustment of the D-guides • Purpose : To adjust the carriage base so that it becomes horizontal to the main unit. • Method : Move up or down the belt stopper which connects between the elevator belt (on the right side) and the carriage base with the eccentric bushing. • Contents : Adjust the height of the movable mounting position at right side against the fixed belt stopper at left side. Adjust the horizontal level of the carriage base so that the difference between the right and left is less than 0.3 mm. • Preparation : Press the Door SW to cancel the operation restriction. Enter Manual elevating operation mode of the Test mode (Diag → Robotics → Individually). Prepare the magazine. (Be sure not to load the upper four discs.) • Adjustment point: Eccentric bushing ∗ Confirm the height of the D guides in advance. Be sure to check the height of the interrupter UP when the adjustment is completed. (1) Move the carriage base to [99]. (2) Rotate the loading motor manually and stop rotating it immediately after the D guides have come out from the carriage base. Do NOT move the chuck outward. (3) Load the magazine into magazine bay No. 2. Care must be taken that the magazine does not touch the D guides. If it does, move back the D guides toward the carriage base. (4) Release the Door switch. (5) While observing through the hole at the top of the magazine, move the carriage base up or down manually so that the slot of disc rack L located to your left and D guide L align. (6) Confirm visually that the difference in height between the slot of the disc rack R on the right side and the D guide R is less than 0.3mm. If not, perform the following adjustment. Note: Do not use the position of the chuck, as it may not be accurate. (7) Loosen the hexagon coupling bolt for fixing, then temporarily tighten it. d (8) If the right side is lower, turn the eccentric bushing counter- clockwise as necessary, and if the right side is higher, turn it clockwise as necessary. (clamping torque: 68.6 Ncm (7 kgcm)) c, d (9) Perform steps (4) to (6) for verification. If the difference still exceeds 0.3mm, repeat steps (7) to (8) and (4) to (6). (10) Lock the screws when the adjustments are completed. g Chuck Left side Right side Fig. 2 Chuck D guide L D guide R Disk rack L Disc rack R www. xiaoyu163. com QQ 376315150 9 9 2 8 9 4 2 9 8 TEL 13942296513 9 9 2 8 9 4 2 9 8 0 5 1 5 1 3 6 7 3 Q Q TEL 13942296513 QQ 376315150 892498299 TEL 13942296513 QQ 376315150 892498299 http://www.xiaoyu163.com 30. Front-Rear Adjustment of the Carriage Base Hexagon coupling Bolt Eccentric Bushing If the right side is lower. If the right side is higher. Fig.3 Right and left horizontal adjustment • Purpose : To adjust the carriage base so that it becomes front-rear horizontal to the main unit. • Method : Adjust by turning the front-rear adjustment screw on the carriage base. • Contents : Adjust the horizontal of the carriage base so that the difference between the front and rear is less than 0.3 mm. • Preparation : Press the Door SW to cancel the operation restriction. Open the rear door and press the Door SW to release the operation limit. Enter Manual elevating operation mode of the Test mode (Diag → Robotics → Individually). Prepare the two magazines. • Adjustment point: Front-rear adjustment screw ∗ Confirm the height of the D guides in advance. Be sure to check the height of the interrupter UP when the adjustment is completed. (1) Move the carriage base to [99]. (2) Rotate the loading motor manually and stop rotating it immediately after the D guides have come out from the carriage base. Do NOT move the chuck outward. (3) Load the magazine into magazine bay No. 2. Care must be taken that the magazine does not touch the D guides. If it does, move back the D guides toward the carriage base.l (4) Release the Door switch. (5) While observing through the hole at the top of the magazine, move the carriage base up or down manually so that the slot of disc rack L located to your left and D guide L align. (6) Remove the magazine, and rotate the loading motor manually so that the D guide moves to the rear. Note: The alarm sound of the disc sensor can be stopped by pressing the FUNCTION button. (7) Set the unit to the state immediately after the D guides come out from the carriage base. Do NOT move the chuck outward. (8) Load the magazine into magazine bay No. 5, and check from the rear that the slot of the disc rack and the D guide align. Confirm visually the horizontal between front and rear from the left and right sides. (9) If there is a difference in height, adjust by turning the front- rear adjustment screw on the carriage base. e (10) If the D guide at the rear side is higher, turn the adjustment screw counterclockwise. If the D guide at the rear side is lower, turn the adjustment screw clockwise. (11) After the adjustment is completed, repeat from Steps 5 to 10 for confirmation, then lock the screws. g Fig. 4 Front-rear adjustment of the carriage base Adjustment screw Carriage base www. xiaoyu163. com QQ 376315150 9 9 2 8 9 4 2 9 8 TEL 13942296513 9 9 2 8 9 4 2 9 8 0 5 1 5 1 3 6 7 3 Q Q TEL 13942296513 QQ 376315150 892498299 TEL 13942296513 QQ 376315150 892498299 http://www.xiaoyu163.com 31. Height Adjustment of the Interrupter UP • Purpose : To align the stop position of carriage base elevation with the disc magazine. • Method : Adjust by turning the interrupter UP adjustment screw. • Contents : Adjust the height of the interrupter UP to align the height at which the carriage base stops with the magazine. • Preparation : Enter Manual elevating operation mode of the Test mode (Diag → Robotics → Individually). Prepare the magazine. (Be sure not to load the upper four discs.) • Adjustment point: Height adjustment screw The LED for monitoring the interrupter output is located on the FCNB Unit (interrupter UP: green). ∗ Confirm the height of the D guides in advance. (1) Move the carriage base to [99]. (2) Manually rotate the loading motor to bring the D guides out to the front. (Set to a state just after the D guides have come out from the carriage base. Do not move the chuck outward.) (3) While observing the green LED, manually move the carriage base slightly up and stop it immediately when the green LED lights up. If the green LED is already lit, first move the carriage base slightly down. (4) When the magazine is slowly inserted, it engages with the D guides just before it locks. While observing through the hole at the top of the magazine, confirm that the D guides are not moved by the magazine. If they move, perform the following adjustment. l (5) If the D guides move, adjust the position of green LED lights up by the interrupter UP height adjustment screw. e (6) Manually set the carriage base to the position where the magazine does not touch the D guides when it moves in and out in the above-mentioned way. → While moving the carriage base up or down little by little, find a position where the D guides do not move even when the magazine is moved in and out. → Find a position of the carriage base relative to the magazine. As this position is used as the reference for adjustment of the interrupter DN, do not move or even touch the carriage base after its position is determined. (7) Turn the interrupter UP height adjustment screw clockwise and stop it when the green LED lights. (If the LED was lit when starting the adjustment, first turn the screw counter-clockwise to go off the LED.) e (8) Further turn the screw 180 degrees (170 to 190 degrees) clockwise then stop it. Encoder side < Detailed explanation > Carriage base side 9.45 mm (9 + phase difference 0.45) 9 mm (pitch 3mm × 3 teeth) Clockwise rotation moves UP Interrupter to upwards. Clockwise rotation moves DN Interrupter to upwards. Clockwise for upwards and counterclockwise for downwards. phase difference / 2 phase difference / 2 A C B A Interrupter Encoder plate UP Lower edge for reference Fig. 5 Adjustment model view DN UP ∗ The interrupters light when the light is blocked. • The figure to the left shows the center of the stop position of the carriage base. The purpose of the adjustment is to obtain this status. The stop position requires A > 0 and B > 0. This means that the stop position range must be ± phase difference/2 and the stop-position range must be equal to the phase difference. Thus, as shown in the figure to the left, set DN (reference side) to phase difference/2 below and UP (adjusting side) to phase difference/2 above with respect to the lower edge of the encoder slit. • Adjust A in the height adjustment. Align the target lower edge of the encoder slit with the position of UP (= the position of the carriage base) [step (7)], then move it up by the amount of A [step (8)]. UP Fig. 5 Height adjustment of the interrupter UP Adjustment screw Carriage base www. xiaoyu163. com QQ 376315150 9 9 2 8 9 4 2 9 8 TEL 13942296513 9 9 2 8 9 4 2 9 8 0 5 1 5 1 3 6 7 3 Q Q TEL 13942296513 QQ 376315150 892498299 TEL 13942296513 QQ 376315150 892498299 http://www.xiaoyu163.com 32. Phase Adjustment of the UP-DN Interrupters Verification of Operations After Adjustments • Purpose : To adjust the stop position range of carriage base elevation to 0.45 mm. • Method : Adjust by turning the Phase-adjustment screw on the carriage base. • Contents : Set the interrupter UP 0.45mm higher than the interrupter DN. Adjust the phase difference (relative height) between UP and DN to 0.45 ± 0.05 mm. • Preparation : Enter Manual elevating operation mode of the Test mode (Diag → Robotics → Individually). • Adjustment point: Phase-adjustment screw The LEDs for monitoring the interrupter outputs are located on the FCNB Unit (interrupter UP: green, interrupter DN: red). (1) Move the carriage base to [99] to permit easy access to the phase-adjustment screw. (2) While observing the green LED, slowly move the carriage base up by hand and stop it immediately when the green LED lights. Important: Be sure to stop the carriage base in an upward movement. (3) Turn the phase-adjustment screw clockwise and stop it when the red LED lights. (If the LED is already lit when starting the adjustment, once turn the screw counterclockwise to turn the LED off.) e (4) Verification: Move the carriage base down until the red LED goes off, then slowly move it up again to check that the two LEDs simultaneously light. If they do not light simultane- ously, repeat the adjustment from step (2). (5) While observing the red LED (interrupter), slowly move the carriage base up or down by hand and stop it immediately when the red LED lights. Be sure to stop the carriage base in an upward movement. (6) In the state when the red LED lights, turn the phase- adjustment screw clockwise 360 degrees (350 to 370 degrees). Be sure to finish the adjustment by turning the phase- adjustment screw clockwise. For example, turn the screw counterclockwise by 390 degrees, then turn it clockwise by 30 degrees to finish the adjustment. (7) Lock the screws when the adjustment is completed. g 9mm 9mm C Clockwise for upwards and counterclockwise for downwards UP UP DN DN < Detailed explanation > ∗ The interrupters light when the light is blocked. Adjust C ( A + B ) in the UP-DN phase adjustments. After aligning the UP interrupter with the lower edge of the encoder slit (step 2), temporarity align the interrupter DN also with the lower edge (step 3). After confirming that the DN and UP interrupters are in place (step 4), align the interrupter DN with the lower edge again (step 5) and move the interrupter DN downwards by the amount of C (step 6). Fig. 7 Adjustment model view Fig. 8 Phase adjustment of the UP-DN interrupters Adjustment screw Height adjustment of the D Guides Right and left, front and back adjustment Height adjustment Relative adjustment of the UP and DN interrupters Verification • Be sure to confirm the height of D guides before the right and left adjustment and front and back adjustment of the carriage base and the height adjustment of the interrupter UP. • Be sure to check the height of the interrupter UP when the right and adjustment and front and back adjustment of the carriage base have been performed. • Perform the relative adjustment of the UP and DN interrupters in conjunction with other adjustments as required. Perform the verification of operations after the height adjustment of the D guides, right and left adjustment and front and back adjustment of the carriage base, height adjustment of the interrupter UP, or relative adjustment of UP-DN interrupters is completed. (1) Set the unit to Manual elevating operation mode of the Test mode (Diag → Robotics → Individually). (2) Move the carriage base to [99]. (3) Set the upper magazine only. (Be sure not to set the upper four discs.) (4) Rotate the turntable in Manual loading operation mode of the Test mode (Diag → Robotics → Individually) to move the D guides out towards the front and rotate the table in the reverse direction to return to a position where the magazine does not touch the D guides. → Set to the state just before the turntable starts rotating. Caution: A manual loading operation may not be allowed, depending on the position of the carriage base or turntable. Be sure to just lightly touch (or momentarily push) the switch when operating it. (5) Observe through the hole at the top of the magazine to check that there is no misalignment in gear teeth or in height between the slot of the disc rack R on the right side and the D guide R or between the slot of the disc rack L on the left side and the D guide L. www. xiaoyu163. com QQ 376315150 9 9 2 8 9 4 2 9 8 TEL 13942296513 9 9 2 8 9 4 2 9 8 0 5 1 5 1 3 6 7 3 Q Q TEL 13942296513 QQ 376315150 892498299 TEL 13942296513 QQ 376315150 892498299 http://www.xiaoyu163.com 33. SENSITIVITY ADJUSTMENT OF THE CARRIAGE-BASE DISC SENSOR • Purpose : To adjust the sensitivity of the disc sensor of the carriage base. • Method : Adjust VR851 on the DSEB Unit • Contents : Adjust the phototransistor output of the light- receiving block. • Preparation : Prepare the adjustment disc. • Adjustment point: Semifixed volume control (VR851, DSEB Unit) Use the asterisk (∗) mark at the lower center of the LCD for monitoring the sensor output. (An asterisk appears when a disc is in.) • How to enter the adjustment mode: (1) Set the door key to UNLOCK position. (2) Press the FUNCTION and ↑→ keys simultaneously for four seconds. (3) "Entering to the Tset Mode!!OK?" is displayed, then press ENT key. (4) Select "Diag" and press ENT key. (5) Select "Robotics" and press ENT key. (6) Select "Collectively" and press ENT key. (7) Select "Step-by-step" and press ENT key. (8) "Source Address ? #001(M1-01)" is displayed. (9) Specify the target address with ←↓ and ↑→ keys and press ENT key. (10) Pull the disc in the carriage block when pressing the ENT key in the display of "Disc Pick-up fwd #xxx". (11) "Dest. Address ? Bay #01" is displayed, then press ESC key. (12) Return the disc to the magazine when pressing the ESC key in the display of "Disc Release rev#xxx". • Adjustment procedure: (1) Set the adjustment disc to the magazine and install the magazine in the location where the work is easy to do. (2) Set the test mode to Step operation mode. (3) Move the carriage base to the address of disc position. (4) Pull the adjustment disc in the carriage base. h (5) Check the display, and turn VR851 on the DSEB unit clock- wise a little when the "disc in" indication is displayed (∗ is displayed in the lower center of LCD), and turn it to the counterclockwise a little when "no disc" indication is displayed. (6) Return the adjustment disc to the magazine. (7) Repeat the steps 4 to 6 until the display of the disc existence changes, and adjust it to be within 10 degrees from the changing point. Fig. 9 Adjustment point DSEB UNIT CN851 R852 J851 IC851 R851 C851 3 GNDD V+5D 5 VR851 GNDD 3 3 DSEB 1 Q851 4 N.C. DSENS SENS 1 1 A O SIDE A VR851 (VR851) Variable control for sensitivity adjustment of the carriage-base disc sensor www. xiaoyu163. com QQ 376315150 9 9 2 8 9 4 2 9 8 TEL 13942296513 9 9 2 8 9 4 2 9 8 0 5 1 5 1 3 6 7 3 Q Q TEL 13942296513 QQ 376315150 892498299 TEL 13942296513 QQ 376315150 892498299 http://www.xiaoyu163.com 34. SENSITIVITY ADJUSTMENT OF THE MAGAZINE DISC OUT-OF-POSITION SENSOR • Purpose : To adjust the sensitivity of the magazine disc out-of -position sensor • Method : Adjust the LED output of the light-emitting block by turning VR852 (FRONT) and VR851 (REAR) on the SIFB2 Unit • Contents : Adjust the voltage by connecting a voltage measuring instrument (voltmeter, multimeter, etc.) to TP851 (FRONT) and TP852 (REAR). • Preparation: (1) Prepare the adjustment disc and adjustment filter. (2) Remove all magazines (including hyper magazine) and drives. (3) Move the carriage base to the initial position (address 3). (4) Connect a voltmeter (or multimeter, etc.) between TP851 (FRONT) or TP852 (REAR) and TP853 (GNDD) on the SIFB2 Unit. • Adjustment point: Semifixed volume control (VR852: FRONT, VR851: REAR) Connect a voltmeter (or multimeter, etc.) to TP851 (FRONT) and TP852 (REAR). • How to enter the adjustment mode: (1) Set the door key to UNLOCK position. (2) Press the FUNCTION and ↑→ keys simultaneously for four seconds. (3) "Entering to the Tset Mode!!OK?" is displayed, then press ENT key. (4) Select "Sensor" and press ENT key. (5) Select "Front sensor" or "Rear sensor" and press ENT key. (6) "Front (Rear) sensor working" is displayed, then the unit enters the disc sensor adjustment mode. Fig. 10 Adjustment points/connections Voltmeter (or multimeter) + W256 R851 C851 R852 R853 R854 R855 R856 C852 R873 R874 Q854 R872 R871 R869 R870 Q853 R868 R867 W224 R882 R883 Q859 VR852 R880 VR851 Q858 R881 W258 CN854 CN855 C856 IC853 W201 W223 W200 W259 W227 CN851 W257 W222 W221 W260 W229 D851 W231 W230 W253 W226 KN851 W225 IC851 W255 W254 W228 REAR 1.V+12 4.XLEDF 3.XLEDR 2.GND12 5.CLK40K DNX2510-B SIFB1 DWX1987-A 437 V0 HC04 1.LEDA+ FRONT 1.LEDB+ 3.LEDB- 3.LEDA- * * DWX2274-A E C B E C B E C B E C B E C B 1 3 R869 VR852 VR851 CN854 W259 REAR FRONT 1.LEDB+ 3.LEDB- 1 3 1 3 1 5 1 7 8 14 SIFB1 UNIT Z REAR (VR851) Variable control for adjustment of the magazine disc out-of-position sensor FRONT (VR852) Variable control for adjustment of the magazine disc out-of-position sensor W109 W151 W111 W110 W108 W148 W149 W150 C855 IC852 CN856 CN860 CN861 C854 C853 R885 R886 R884 R888 R887 R892 R893 R894 R895 R891 R890 R889 IC854 KN852 W153 D852 W113 C857 W112 W152 W135 W134 W133 TP853 W136 CN857 R899 CN858 R897 R898 C860 C861 SIFB2 3.XDROF DWX1990-A DNX2513-A 1.FRONT 1.V+12 2.GND12 3.XSECS HC165 4.CLK3 437 V0 5.SESI 1.XDROR 1.GNDD 2.GND12 3.DOR 2.V+5D 1.GNDD 4.GND12 2.GND 3.REAR 3.DOF 2.V+5D * * +5V GND IN OUT 1 8 9 16 1 5 1 3 1 3 1 4 1 3 SIFB2 UNIT AE FRONT FRONT REAR REAR GNDD GNDD FRONT REAR GNDD TP851 TP852 TP851: FRONT TP-Point TP852: REAR TP-Point TP853: GND TP-Point SIDE A SIDE A • Adjustment procedure: (1) Set the test mode to disc sensor adjustment mode. (2) Set the adjustment disc and adjustment filter so that it blocks the optical axis. (Insert the adjustment disc and filter to slot 50 of the magazine and set to magazine bay #3 at the front side and set to magazine bay #7 at the rear side.) h i (3) Adjust VR852 (FRONT) and VR851 (REAR) on the SIFB2 unit so that the voltage of TP851 (FRONT) and TP852 (REAR) become the adjustment value which is mentioned on the case of the adjustment disc (toletrance: ± 0.2V). COM + www. xiaoyu163. com QQ 376315150 9 9 2 8 9 4 2 9 8 TEL 13942296513 9 9 2 8 9 4 2 9 8 0 5 1 5 1 3 6 7 3 Q Q TEL 13942296513 QQ 376315150 892498299 TEL 13942296513 QQ 376315150 892498299 http://www.xiaoyu163.com 35. ELEVATING SPEED ADJUSTMENT • Purpose : To adjust the elevating speed of the carriage base. • Method : Adjust VR601 on the VMDB Unit • Contents : Adjust the pulse width of TP601 (MMOUT). • Preparation : Connect an oscilloscope (10:1 probe) to TP601 (MMOUT) and TP602 (GND) on the VMDB Unit. • How to enter the adjustment mode: (1) Set the door key to UNLOCK position. (2) Press the FUNCTION and ↑→ keys simultaneously for four seconds. (3) "Entering to the Tset Mode!!OK?" is displayed, then press ENT key. (4) Select "Diag" and press ENT key. (5) Select "Robotics" and press ENT key. (6) Select "Individually" and press ENT key. (7) Select "Elevation" and press ENT key. (8) Select "Manual" and press ENT key. (9) Carriage base moves to up and down with ←↓ and ↑→ keys and generates a pulse from the rotary encoder. • Adjustment procedure: (1) Set VR601 on the VMDB Unit to the mechanical center. (2) Turn the elevating motor by using the elevating manual operation and generate a pulse from the rotary encoder. (3) Adjust VR601 so that the pulse width of TP601 (MMOUT) to 13 ± 0.3 msec. Caution: Be carful because the carriage base is moved at high speed in some modes. VMDB UNIT W W167 W174 W163 W164 W189 W142 W165 H601 W103 W285 D613 Q613 Q614 R685 R686 R684 Q611 R683 Q612 D612 CN601 C601 CN602 R602 R603 R601 C602 R605 R604 IC601 IC602 VR601 C604 C603 C606 C605 R606 D601 TP601 C608 C607 C609 C610 R609 R610 R607 R608 IC603 R613 R614 R617 R615 R616 C613 IC605 R618 R619 C614 C615 C616 R620 C618 C619 R621 R622 C617 R623 R625 R624 R611 R612 C611 C612 IC604 IC606 IC617 CN604 CN605 C620 R670 Q608 IC614 Q609 R671 R672 R675 R673 R674 C642 D608 Q607 Q610 D609 D610 R626 IC612 R627 R628 R629 C624 R636 R635 R637 R634 Q602 R633 R632 Q601 R631 C622 R630 IC613 D611 C643 R677 C644 C645 C647 C648 R676 R679 R680 R678 R681 R682 C646 IC608 R638 C626 IC609 C625 IC610 R668 D602 C641 IC607 R669 R667 R665 R664 R666 R663 R662 R661 C640 C639 D603 D604 D605 R639 R640 R641 R642 C627 R643 R644 Q604 Q606 Q603 Q605 C628 C629 C630 R650 R645 R646 R652 R653 R651 R647 R649 R656 R659 C637 C638 R660 IC611 D606 D607 C621 C623 C631 C633 C632 R648 C634 C635 R654 R655 C636 R657 R658 IC615 L601 C649 D614 C650 W194 C651 IC616 RY601 C652 D615 RY602 C653 D616 D617 RY603 C654 CN608 D619 D620 Q617 Q615 Q616 R687 R688 Q618 CN609 D621 D622 Q622 Q623 Q624 Q620 R689 R690 Q625 Q626 Q621 Q619 CN606 L602 C655 C656 C657 CN607 W235 W263 W155 W204 W129 W143 W240 W195 W208 W198 W216 W171 W219 W117 W278 W239 W203 W272 W101 W283 W197 W273 W274 W116 W114 W269 W246 W266 W270 W217 W218 W276 TP602 W215 W214 W244 W173 W144 W145 W243 W248 W250 W284 W105 W130 W279 W280 W209 W183 W185 W137 IC620 W232 W157 W169 W236 W286 W177 W237 W206 W205 W220 W210 W187 W123 W122 W146 W212 W262 W193 W186 W199 W275 W271 W121 W141 W118 W119 W115 W234 W120 IC619 W190 W126 W127 W170 W192 W102 IC621 H602 KN601 W147 CN612 W131 KN602 W107 W238 W124 W168 W140 L603 C659 W249 W251 W132 W252 W264 W282 W265 W268 W242 W267 W166 W125 W128 W138 W154 W156 W159 W158 W196 W161 W139 W162 W184 W181 W178 W179 W182 W172 W175 W176 W207 W188 W213 W211 W233 W202 W277 W261 W241 W281 W245 W104 W106 W247 W160 TH601 W180 W191 ICP-N50 4565D 10393 ICP-N10 HC14 15 3.GND12 1.XDSWF 3.GND12 2&4.GND12 1.XDROR 1.XDSWR 3.XDROF 1.VMD+ 2.GND 1.V+5 2.VMD- 3.XUP 5.VMPWM SBRK 4.SBRK 6.VOA 9.XPLCNT1 8.VMLOCK 7.VOB 10.XPLCNT2 13&14.VSWD15 12.N.C. 11.CLK20K 15&16.GND15 19&20.GND12 17&18.VSWD12 4.GNDD 3.PLR- 3.PLF- 1.PLF+ 1.PLR+ 2.V+24 1.GND24 DNX2504-A ICP-N50 DWX1981-A HC86 HC04 HC123 10393 437 V0 VMDB MMOUT GND 3.GND12 4.V+12 5 10 VMPWM MMOUT 1.V+5V 3.VOB 2.VOA 4565D 4565D 10339 4565D ICP-N38 HC32 HC11 FU601 V+12V GND12 V+5V GNDD V+12V GND12 V-12V * * * * * * * * * * * * * * * * 1 1 SAME TYPE AND RATING OF FUSE RISK OF FIRE, REPLACE ONLY WITH CAUTION-FOR CONTINUED PROTECTION AGAINST E C B E C B E C B E C B E C B E C B E C B E C B E C B E C B E C B E C B E C B E C B 1 3 4 8 1 3 4 8 1 3 4 8 E C B E C B E C B E C B E C B E C B E C B E C B E C B E C B E C B E C B 1 4 1 2 19 1 20 1 4 1 7 8 14 1 8 9 16 1 4 5 8 1 4 5 8 1 7 8 14 1 4 5 8 1 9 1 3 1 3 1 4 5 8 1 7 8 14 1 4 5 8 1 7 8 14 1 7 8 14 1 7 8 14 1 4 5 8 1 10 1 3 1 3 1 4 C602 IC602 C606 C605 R606 D601 TP601 R607 C614 C61 W216 W269 W270 W217 W218 TP602 W271 W247 HC123 MMOUT GND * * B 1 8 9 16 8 VR601 Fig. 11 Adjustment point/connections Oscilloscope GND Probe (10:1) (VR601) Variable control for adjustment of elevating speed TP-601: MMOUT (TP-Point) TP-602: GND (TP-Point) SIDE A www. xiaoyu163. com QQ 376315150 9 9 2 8 9 4 2 9 8 TEL 13942296513 9 9 2 8 9 4 2 9 8 0 5 1 5 1 3 6 7 3 Q Q TEL 13942296513 QQ 376315150 892498299 TEL 13942296513 QQ 376315150 892498299 http://www.xiaoyu163.com 36. DRM-3000 LCD POWER SUPPLY VOLTAGE ADJUSTMENT • Purpose : To adjust the power supply voltage of the LCD module. • Method : Adjust VR701 on the FRPB Unit • Contents : Connect a voltmeter (or multimeter, etc.) between CN702-pin 2 (VEE) and pin 1 (VSS), and adjust the voltage. • Preparation: (1) Remove the FRPB Unit from the front panel. (LCD module and key SW unit are unnecessary.) (2) Connect the power supply of 12V ± 5% between CN701-pin 1 (V12) and pin 2 (GND12), and connect the voltmeter between CN702-pin 2 (VEE) and pin 1 (VSS). • Adjustment procedure: Semifixed volume control (VR701) Connect the voltmeter (or multimeter, etc.) between CN702- pin 2 (VEE) and pin 1 (VSS). (1) Set VR701 on the FRPB unit to the mechanical center. (2) Apply a 12V power supply. (3) Adjust VR701 so that the voltage of CN702-pin 2 (VEE) becomes 5 ± 0.05V. C701 C708 C703 R708 R711 C709 C711 C712 R735 W127 C706 R732 R733 IC704 IC705 R709 R710 R712 C705 C707 R743 R745 R744 Q718 Q719 VR701 BU701 S701 S702 S705 S704 S703 R714 D701 C704 IC703 R715 Q701 D702 R716 Q702 D703 R717 D704 Q703 R756 R755 R753 R754 R751 R752 R750 R749 R701 R702 R703 R704 R705 C702 R720 W122 W132 W156 W135 W141 W133 W103 W154 W160 W157 W144 W114 W155 W162 W159 W123 R723 W152 W110 W104 W102 C717 W101 W116 R722 W117 W161 J701 R734 C716 C720 C719 W113 W146 W145 C715 W151 CN701 C721 C722 W115 W149 CN712 W119 W128 W120 W142 W150 W147 C718 W124 W136 R713 W129 W118 W107 W131 W148 W125 W121 W134 W140 W111 W126 W108 W112 W130 W105 W137 W138 W139 W158 CN703 CN702 R719 R707 R718 D705 IC701 R706 W143 W153 W106 W109 GND12 V+5V V+5V GNDD GNDD GNDD 2.N.C. DB0 * DB3 V+12V DB1 DB2 DB5 * * * DB7 ILED * IRET DB6 3 DB4 * * * 437 V0 10 5 LCDE R/XW LCDRS VEE 5 1 3.GNDD 1.KEY V+5D GNDD 13.IRET 10.KEYSI 9.XKEYCS 8.OE 7.SDO 6.CLK3 5.XFRCS 4.GNDD 12.LCDE 11.LCDRS 3.V+5V 13 1 2.GND12 1.V+12V FRPB DWX1996-A DNX2519-A ESC L R ENT FUNCTION POWER DRIVE BUSY BUSY ROBOTICS MAILSLOT OCCUPIED * * E C B E C B M G F 1 2 3 E C B E C B E C B 1 4 0 1 4 0 IN OUT 1 8 9 16 1 8 9 16 F M G 1 8 9 16 0 1 4 0 1 4 1 10 1 6 C706 R732 R733 C707 VR701 R720 W157 W159 C716 C715 W158 R719 R707 R718 IC701 IN OUT W160 R713 CN702 D705 V+5V * LCDE R/XW LCDRS VEE V+5D GNDD 1 6 FRPB UNIT AP Voltmeter (or multimeter) + CN702: 2pin (V+5D) (TP-Point) CN702: 1pin (GND) (TP-Point) VR701 Variable control for adjustment of LCD power supply voltage SIDE A Fig. 12 Adjustment points/connections COM + www. xiaoyu163. com QQ 376315150 9 9 2 8 9 4 2 9 8 TEL 13942296513 9 9 2 8 9 4 2 9 8 0 5 1 5 1 3 6 7 3 Q Q TEL 13942296513 QQ 376315150 892498299 TEL 13942296513 QQ 376315150 892498299 http://www.xiaoyu163.com 37. GENERAL INFORMATION DIAGNOSIS SYSTEM ADMINISTRATOR MODE Turn the door key to UNLOCK, then press the FUNCTION key. Model name and serial number ENT Bay configuration check Magazine type, ID number Drive model name, SCSI ID, termination, serial number ENT Maintenance information Log: error log, loaded disc numbers Contents: Slot data of the disc magazines Run-statistics: Operation time (Power ON/ Drive work) Operation number (elevation/ load & unload/ mailslot/ Hyper/Flip) ENT Disc change, removal, and addition ENT Ejection of the Hypermagazine ENT Probe on the designated magazine ENT Opening of the door After selecting "Front," press the ENT key. → The front door is open. After selecting "Rear," press the ENT key. → The rear door is open. After selecting "Both," press the ENT key. → Both doors are open. ENT To Option submode (Refer to "Option Submode".) ENT www. xiaoyu163. com QQ 376315150 9 9 2 8 9 4 2 9 8 TEL 13942296513 9 9 2 8 9 4 2 9 8 0 5 1 5 1 3 6 7 3 Q Q TEL 13942296513 QQ 376315150 892498299 TEL 13942296513 QQ 376315150 892498299 http://www.xiaoyu163.com 38. Option Submode The changer automatically detects a disc magazine that needs probing, and executes detection of whether or not a disc is loaded. (Default: OFF) ENT If a disc is in a drive, the changer does not return it to the magazine when the power is turned on. (Default: OFF) The tray of the mailslot does not open automatically. The Hypermagazine is not automatically ejected. (Default: ON) The Hyper magazine is regarded as the mailslot. (Default: ON) The alert buzzer sounds if trouble occurs. (Default: ON) Free messages from the host computer are displayed. (Default: OFF) The device name of the changer is changed to DRM-7000. (Default: DRM-3000) Warning messages are displayed if any abnormality is generated in the fans inside the changer. (Default: ON) www. xiaoyu163. com QQ 376315150 9 9 2 8 9 4 2 9 8 TEL 13942296513 9 9 2 8 9 4 2 9 8 0 5 1 5 1 3 6 7 3 Q Q TEL 13942296513 QQ 376315150 892498299 TEL 13942296513 QQ 376315150 892498299 http://www.xiaoyu163.com 39. TEST MODE Entering Test Mode (1) After the power is turned on and the initialization of the mechanism ("Initializing" is displayed) is completed, the following indication is displayed. (2) Set the door key to UNLOCK and press the FUNCTION key. The following indication is displayed: (3) Press the FUNCTION and ±= keys simultaneously for 4 seconds. The following indication is displayed: The unit is in User mode. The unit enters System Administrator mode. Asking if you wish to enter Test mode. (4) Press the ENT key. The following indication is displayed: The unit enters Test mode. The cursor is blinking on D (Diag). Diag mode • Select "Diag," then press the ENT key. (5) Move the cursor to the mode of your choice by pressing the ±= or +≠ key, then press the ENT key. (Elevation Manual operation mode/ Auto operation mode) • Elevation Manual/Auto (Loading Manual operation mode) • Loading Manual/Auto (Flip-unit Manual/Auto operation mode) • Flip-unit Manual/Auto (Clamper Manual operation mode) • Clamper Manual/Auto (Mailslot Manual/Auto operation mode) • Mailslot Manual/Auto (Hyper magazine Manual/Auto operation mode) • Hyper-Mag. Manual/Auto Diagnosis of each section Step-by-step check of a series of operations Selection of a slot and drive ENT Check of the disc out-of-position sensor Adjustments of the front and rear sensors are executed separately. ENT Check of the changer interface Clamp motor, clamp switch Clamping-completed signal, Spindle-stop signal ENT ENT ENT ENT www. xiaoyu163. com QQ 376315150 9 9 2 8 9 4 2 9 8 TEL 13942296513 9 9 2 8 9 4 2 9 8 0 5 1 5 1 3 6 7 3 Q Q TEL 13942296513 QQ 376315150 892498299 TEL 13942296513 QQ 376315150 892498299 http://www.xiaoyu163.com 40. Preparation : Set two discs into Disc slots #001 and #350. Modifiable setting items : • Disc slot number for the first disc (Default: #001) • Disc slot number for the second disc (Default: #350) • Bay number of the drive unit (Default: Bay #4) Note: The modified settings will be retained until the power is turned off. OK Set If the disc is in the flip-box, "–– Flip ––" is displayed. "CYC" indicates the number of cycles (max.: 999999), and the approximate time for changing discs. Note 1: In the following cases, the setting will not be accepted: • When a specified magazine is not installed. (Even the default setting will not be accepted if the magazine is not installed.) • When a disc has been set in the specified drive unit. Note 2: The approximate time for changing discs is calculated according to the time from just after the spinning-stop process is completed until just before the spinning-start process is started. (Although the drive is not controlled in this mode, the time just before a drive-control command is processed is included.) The time is rounded off to two decimal places. Note 3: If the specified disc is not set in the specified magazine, error EF8 is generated. To restart the operation without clearing the cycle number, press ENT. To interrupt this mode, press ESC . ENT Any bay number with no drive unit is displayed and can be assigned. This indication is only displayed when a Flip-box is recognized. Press ENT key to display the Flip-Box Setting OK/Set screen. Demo 2 Indications ENT ENT Operational steps : (1) The disc in slot #001 is carried to the rear Bay #4 drive unit. (2) The disc in the rear Bay #4 drive unit is returned to slot #001. (3) The disc in slot #350 is carried to the rear Bay #4 drive unit. (4) The disc in the rear Bay #4 drive unit is returned to slot #350. Note: The above steps (2) to (4) constitute one cycle. Specifications of Demo mode (1) Move the cursor to Demo by pressing the ± key, then press the ENT key to display the Demo Mode Select screen. Select Demo 1, 2 or 3 mode by pressing the ±= or +≠ key. (2) Press the ENT key to enter the demo mode you have selected. Preparation : Set 8 discs each into Hyper magazines #1-8 (from the lowest to the 8th slots). Operational steps : (1) The disc in Hyper magazine #1 is carried and inserted into the rear Bay #1 drive unit. (2) The disc in Hyper magazine #2 is carried and inserted into the rear BAY #2 drive unit. (8) The disc in Hyper magazine #8 is carried and inserted into the rear Bay #8 drive unit. (9) All the transferred discs start rotating. Demo 1 completed. In this mode, a disc is carried to the drive unit, the drive unit is started, then stops. Discs must be set in Hyper magazines #1 to #8. Demo 1 OK In this mode, two discs are carried one after another to one drive unit. Two discs are required. Demo 2 In this mode, discs are carried to all magazines installed, one after another. Discs must be set in Hyper magazines #1 to #4. A disc is being carried to the drive unit. Note: If a drive unit is not installed at the rear Bay, the disc is carried to the location where the specified drive unit should be installed then returned to the original Hyper magazine. Operation completed. Operation completed. Demo 3 Demo 1 Indications : ±= +≠ ±= +≠ www. xiaoyu163. com QQ 376315150 9 9 2 8 9 4 2 9 8 TEL 13942296513 9 9 2 8 9 4 2 9 8 0 5 1 5 1 3 6 7 3 Q Q TEL 13942296513 QQ 376315150 892498299 TEL 13942296513 QQ 376315150 892498299 http://www.xiaoyu163.com 41. OK Set A disc is being carried from the Hyper magazine to the Minimum magazine. Note: "OK" is not accepted if the Hyper magazines are not inserted. The disc slot numbers from and to which the disc is being carried and the round number are displayed. The left round number is the current round number. A disc is being carried from the Minimum magazine to the Hyper magazine. Hyper magazines prepared. Select whether you wish to continue or return the discs to the Hyper magazines. You can also select "Infinity". Specified number of rounds completed. All discs have been returned to the Hyper magazines. If the operation is interrupted, and discs are returned to the Hyper magazines: Demo 3 Indications : To interrupt this mode, press ESC . Preparation : • Set four discs each into Hyper magazine #1 to #4 (from the lowest to the fourth slots). • Discs should not be inserted into other Hyper magazines. Operational steps : (1) The discs in Hyper magazine #1 to #4 are carried to Minimum magazine #1 to #4. (2) The disc in Minimum magazine #3 (the second disc from the top) is carried to the Hyper magazine #5. (3) The disc in Minimum magazine #1 (the lowest disc) is carried to Hyper magazine #3. (4) The disc in Minimum magazine #4 (the upper disc) is carried to Hyper magazine #6. (5) The disc in Minimum magazine #2 (the third disc from the top) is carried to Hyper magazine #4. Note: Reverse steps (2) through (5) above, and when all discs return to Minimum magazine #1 to #4, one round is completed. Repeat this for the 2nd round. (6) The discs in Minimum magazine #1 to #4 are carried to Hyper magazine #1 to #4. Modifiable settings : • Possible number of rounds: 1 to 999 (default: 2 rounds). Infinity can be also assigned. Note: The modified setting is retained until the power is turned off. www. xiaoyu163. com QQ 376315150 9 9 2 8 9 4 2 9 8 TEL 13942296513 9 9 2 8 9 4 2 9 8 0 5 1 5 1 3 6 7 3 Q Q TEL 13942296513 QQ 376315150 892498299 TEL 13942296513 QQ 376315150 892498299 http://www.xiaoyu163.com 42. Elevation mode Press the ENT key. After selecting "Manual," press the ENT key. After selecting "Auto," press the ENT key. While the cursor key is held pressed, elevation operation is possible. While the cursor key is held pressed, loading operation is possible. The carriage base repeats moving upwards/ downwards between the lowest and highest positions. (To stop operation, press the ESC key.) Loading mode Press the ENT key. "Auto" cannot be selected. After selecting "Manual," press the ENT key. While the cursor key is held pressed, mailslot operation is possible. Press the ENT key. After selecting "Manual," press the ENT key. After selecting "Auto," press the ENT key. Mailslot mode The unit repeats opening/closing. (To stop operation, press the ESC key.) Elevation Manual / Auto ? Elevation. will Be selected ? Elevation. Elev : Loading Manual / Auto ? Loading. will Be selected ? Loading. V: OK SW : 11100 Mailslot Manual / Auto ? Mailslot. will Be selected ? Mailslot. Mailslot :. 0003 0001 Close 0001 www. xiaoyu163. com QQ 376315150 9 9 2 8 9 4 2 9 8 TEL 13942296513 9 9 2 8 9 4 2 9 8 0 5 1 5 1 3 6 7 3 Q Q TEL 13942296513 QQ 376315150 892498299 TEL 13942296513 QQ 376315150 892498299 http://www.xiaoyu163.com 43. TROUBLESHOOTING 1. Basic Concepts ENT FUNCTION FUNCTION (Check if it is the UNLOCK status.) 0 1 When no disc remains in the drive When a disc remains in the drive A condition in which normal changer operation cannot be continued is defined as "error status." When SCSI commands are used for operations, a check condition is returned to the host computer if an illegal command is sent. However, if normal operation can be executed by sending a legal command, this is not "error status." An error with which operation of the disc-carriage mechanism cannot be continued is called a "fatal error." When a fatal error occurs, the error status cannot be released even if you turn the power off and on again. This is intended to eliminate secondary damage to the disc or the mechanism caused by starting initialization without removing the cause of the error. Be sure to open the door and check the internal condition of the changer to find the cause of the error, and take appropriate action. Initialization will start when the door is closed. 2. Indication and Buzzer upon Error Generation If an error is generated, the buzzer sounds in synchronization with flashing of the backlight of the display window. In the display window, the "Error code and its explanation" and "Detailed information" are alternately displayed in an interval of 2 seconds. The buzzer stops sounding when the ESC key is pressed, but no subsequent operation can be performed without first operating the Lock Release key. This means that the operation to release the error can be performed only by the system administrator who manages the key or by service personnel. 3. Operation Guidance upon Fatal Error Generation As the door needs to be opened, one-touch shift to Door submode of System-administrator mode is enabled. (Check whether it is the UNLOCK status.) When the front door opens: When the rear door opens: ENT ENT When the rear door opens: When the front door opens: ±= ±= When a disc is used in the drive, the drive can be used even if an error occurs in the disc carriage mechanism. However, the door cannot be opened without stopping the drive. The system administrator should determine which takes priority, error canceling or continued use of the drive. • If the host computer is connected, issue a "Rezero Unit" command. The drive will stop, and the unit will shift to Door submode. The disc will not be returned. • If the host computer is not connected, turn off the power, then turn it on again. • Detailed information on errors (1) Error code (in hexadecimal notation) (2) Table number (in hexadecimal notation) (3) Sequence step (in hexadecimal notation) From the data (2) and (3), a mechanical sequence when an error was generated can be assumed. (4) Address where the error was generated (in hexadecimal notation) An error generated while a disc is moved between magazines can be also specified (indicated with the physical address). (5) Elapsed time when the error was generated (in decimal notation) A total of hours from the time when the system was turned on until the error was generated is displayed in hours and minutes. (In the LCD, the indication is in hours.) • Even if the same error was generated continuously, all errors are recorded in the error log. E** fatal level *********** E** (** - ** - **) **** ****** hour • The Table Number may become "00 " if an error is generated in DEMO mode. www. xiaoyu163. com QQ 376315150 9 9 2 8 9 4 2 9 8 TEL 13942296513 9 9 2 8 9 4 2 9 8 0 5 1 5 1 3 6 7 3 Q Q TEL 13942296513 QQ 376315150 892498299 TEL 13942296513 QQ 376315150 892498299 http://www.xiaoyu163.com 44. ENT (Check whether it is the UNLOCK status.) When an error occurs during mechanism initialization: (Check whether it is the UNLOCK status.) Select YES then ENT . When an error occurs in a mode other than mechanism initialization: Hyper-magazine timeover ENT (Check whether it is the UNLOCK status.) Select NO then ENT . 4. Quitting from Nonfatal Error Status (Mainly Errors with the Drive) FUNCTION FUNCTION FUNCTION • If the indication returns from "Initializing" to an error indication again, it is necessary to manually open the door and remove the drive that caused the trouble. Following "7.1.8 DISASSEMBLY", open the rear door, disconnect the drive mounted on the drive bay (Bay 1 to Bay 8) having the corresponding number to the suffix (0 to 7) of the error code, then remove it. When you close the door, initializing of the mechanism begins. • Sufficient care must be taken when checking the drive, since disconnecting/reconnecting the changer interface is equivalent to disconnecting/reconnecting the entire drive unit. • If a disc remains in the removed drive, manually take it out. NEVER return the drive with a disc remaining inside to the changer. As the disc is not detected, and this may cause a secondary problem. • The requirements and operation procedure when the indication returns from "Initializing" to the previous error indication are the same as those "when an error occurs during mechanism initialization," mentioned above. • When you specify "Initializing No.," Inquiry submode is selected. Change to Door submode to open the door, and remove the defective drive. • If the memory of a hyper magazine cannot not be read, a warning message is displayed. Error EE0 is generated by a timeout in an inserting/ejecting operation, which has no relationship to memory. In either cases, normal condition may be restored by ejecting the hyper magazine and then reinserting it. www. xiaoyu163. com QQ 376315150 9 9 2 8 9 4 2 9 8 TEL 13942296513 9 9 2 8 9 4 2 9 8 0 5 1 5 1 3 6 7 3 Q Q TEL 13942296513 QQ 376315150 892498299 TEL 13942296513 QQ 376315150 892498299 http://www.xiaoyu163.com 45. 5. Preparatory Operations after Opening the Door, and Related Cautions 6. Check Items and Management Procedure for Each Error Code When the door opens, push the FUNCTION key to switch to System Administrator mode and read out and make a note of various kinds of information upon error generation in Config submode and Info submode. It will be useful for future error analysis and management. • Mount position of magazine (bay number), magazine ID, and magazine type : Read out in Config submode. • Mount position of drive (bay number), device ID, SCSI ID, Term and drive type : Read out in Config submode. • Error log (error code, detailed information) : Read out using "Log/Error-log" in Info submode. • Running time, the number of times of operation : Read out using "Run-statistics" in Info submode. • Whether the machine recognizes whether there is a disc in the changer : Read out using "Contents" in Info submode. Error log display To see the "Error code and its explanation" of an error, select the desired error from the error log list, and press the ENT key. If the ENT key is pressed again, "Detailed information" is displayed. To return to the previous display, press the ESC key. "Error log list" "Error code and its explanation" "Detailed information" If a magazine or a drive obstructs the view of the disc carriage mechanism when the door is open, pull out the magazine or the drive, as required. However, to recover the unit surely and quickly after error correction, follow the notes shown below: • The operation must be done with the power on, as connecting and disconnecting of devices are not recognized when the power is off. • Make a note of the bay and magazine numbers when you pull out the magazine, and return the magazine to the original position when reconnecting it after error management. • If a disc remains in the disconnected drive, be sure to take out the disc. If the drive is reconnected to the changer with a disc remaining, the disc is not detected, and this may cause a problem. • Mechanism Initialization may begin if the door is closed. Be careful not to inadvertently close the door during operations. Blocking the hole to disable the door switch may be effective. • You can check the operation while observing the internal mechanism with the door open by pressing the door switch. In this case, be careful not to insert anything such as your hands inside, because the carriage base travels at high speed. And do NOT connect/disconnect the magazines and drives in this condition. As such a situation is impossible under normal conditions, doing so may generate inconsistency and cause a secondary problem. • Do NOT eject the disc from a magazine. Doing so may cost you unnecessary probing operations after error management. Fatal errors (mainly errors with the mechanism) Confirmation of the causes and management procedure Disc-protruding errors Error No. LCD Display Most Likely Causes Check Items Management Procedure E83 disc set NG Disc protruding The disc-protruding sensor becomes active when the door is opened, and the buzzer keeps sounding while trouble persists. Pull out the connected magazines one by one until the buzzer stops. (The hyper magazine is ejected in Hyper submode.) If the buzzer stops sounding when a magazine is ejected, that magazine is the cause of trouble. Check whether the disc is tilted or not. The error will be canceled if the buzzer does not sound after inserting the disc again properly and mounting the magazine again. Chuck mechanism protruding If the buzzer keeps sounding even after you remove all the magazines, check whether the carriage base block is in proper condition. If the chuck or D-guide of the carriage base block is protruding, rotate the pulley on the rear side with your fingers (take care that the belt does not come off) so that the chuck or D-guide returns to its normal position. The error will be canceled if the buzzer turns off. Defective sensor If the buzzer keeps sounding even after the carriage base block returns to the normal position, check that the light sensor is not blocked and nothing is stuck to it. If you find nothing blocking or stuck to the light sensor block, close the door and try initialization. If the buzzer does not stop, readjustment of the sensor sensitivity is needed. Error code (hex) Detailed information display E ∗ ∗ (∗ ∗ - ∗ ∗ - ∗ ∗) ∗ ∗ ∗ ∗ ∗ ∗ ∗ ∗ ∗ ∗ hour Table number (hex) Sequence steps (hex) Elapsed time when an error was generated (in hours) Physical address (hex) Caution: As the carriage base operates at a high speed, do NOT insert anything, such as your hands, inside. www. xiaoyu163. com QQ 376315150 9 9 2 8 9 4 2 9 8 TEL 13942296513 9 9 2 8 9 4 2 9 8 0 5 1 5 1 3 6 7 3 Q Q TEL 13942296513 QQ 376315150 892498299 TEL 13942296513 QQ 376315150 892498299 http://www.xiaoyu163.com 46. Errors in the elevating system After an error is generated in the elevating system, manual operation (Diag-Robotics-Individually-Elevation-Manual in Test mode) is also forbidden, because there is no guarantee that the address will be recognized normally. However, by setting to this mode, you can monitor the change in address using the display window. When an error is generated, set the unit to this Test mode first. Error No. LCD Display Most Likely Causes Check Items Management Procedure E8A undefined error Disc out-of-position sensor The output from the disc out-of- position sensor may be incorrect during initialization immediately after the power is turned on. Turn the unit off then back on to reinitialize it. E87 elev. sensor Elevating address sensor trouble Remove the side panel (right side), and check the lighting state of the green and red LEDs on the FNCB unit or DCMB1 unit. The carriage base moves up or down as you rotate the pulley or belt of the VD motor. The LEDs show the VUPS and VDNS logic. If they turn ON/OFF normally, the MMCB unit is defective. Check whether pins 84 and 86 of IC101 are stable. E88 elev. motor lock Elevating motor locked Pull out the magazines, confirm the position of the carriage base, and check that it corresponds to the address recognized by the changer (read out in Test mode). If the position corresponds to the address properly, close the door and try initialization. If the machine does not work, and E88 is generated again, remove the side panel (right side), and check that CN105 of the MMCB unit is not disconnected. VMLOCK at pin 8 of CN105 is Low in normal condition. If VMLOCK remains High when the VD motor is not driven, there is a wire disconnected. Elevating address sensor or rotary encoder trouble If the recognized address does not correspond to the actual position of the carriage base, and the carriage base is located in the highest or lowest position, there may be sensor trouble. Remove the side panel (right side), and check the same items as those for E86 and E87 while moving the carriage base by rotating the pulley or belt of the VD motor. Foreign object contamination If the carriage base is located in the highest or lowest position, something may have gotten caught inbetween. Remove the side panel (right side), and try to move the carriage base by rotating the pulley or belt of the VD motor. Move it slightly in the movable direction, and remove the foreign object, if any is found. E89 elev. timeover (Normal timeout value is set to 10 seconds.) Belt off in the elevating drive unit Press the door switch without closing the door. If the unit does not work, and E89 is generated, remove the side panel (right side) and check the elevating drive unit (timeout value is set to 65 seconds for initialization). You can see the elevating drive unit by removing the side panel (right side). Check the transfer system (such as the belt) from the VD motor to the carriage base. Be careful not to touch the carriage base because it travels at high speed. Adjustment inaccuracy If E89 is generated after an elevation-initializing operation toward around address 15 is completed, check that the carriage base is not jolting up and down around address 3 or 15. Even when the carriage base reaches around the target address in 10 seconds, a timeout occurs if it cannot accurately find the stop point and jolts up and down. Check whether the adjustment of the carriage base is accurate. Installation error or deformation of the encoder plate, or attachment of foreign objects to it If E89 is generated in an elevating operation to a particular address when an initializing operation is completed normally, check the current address of the carriage base in Test mode. Also check the lighting statuses of the green and red LEDs on the FNCB unit. There may be a problem with the encoder slit around the address. Try an elevating operation to the suspected address using "Diag-Robotics-Collectively-Step by step" (Step Operation mode) in Test mode. www. xiaoyu163. com QQ 376315150 9 9 2 8 9 4 2 9 8 TEL 13942296513 9 9 2 8 9 4 2 9 8 0 5 1 5 1 3 6 7 3 Q Q TEL 13942296513 QQ 376315150 892498299 TEL 13942296513 QQ 376315150 892498299 http://www.xiaoyu163.com 47. Errors in the loading system The loading motor can be operated manually (Diag-Robotics-Individually-Loading-Manual in Test mode) only if you cancel the operation restriction by pressing the door switch (turning the relay on). Be sure to switch to Test mode first, because initialization (including the elevating system) is started when the door switch is pressed in any mode other than Test mode. (Initialization is not started by closing the door after switching to Test mode). In addition, be sure to press the door switch with the door open, because operating the motor without observing the change in the mechanism status may cause a secondary problem. Error No. LCD Display Most Likely Causes Check Items Management Procedure E97 loading SW NG Dislodged or disconnected flexible cables Check whether the change in the mechanism status corresponds to the logic change of the switches by rotating the pulley on the rear side manually while monitoring the logic of the five loading switches with "Diag- Robotics-Individually-Loading- Manual" in Test mode. If the logic of the switches does not change, remove the right side panel, and check whether the flexible cable connection from the MMCB unit to the carriage base is normal. If any disconnected cable is found, reconnect it after turning the power off. Removal of the switch arm in the carriage base block If the logic of the switches does not change while connection of the flexible cable is normal, check the switch arm mounted on the bottom of the carriage base block. If the switch arm is not located at the correct position, it may have dropped somewhere inside. This may cause E88. Find and remount it to the correct position. Replacement of the MMCB unit If the MMCB unit is replaced with a new one, an error is generated when the unit is turned on for the first time after replacement. Quit from error status, then turn the unit off then back on. E98 loading mecha NG Grease shortage around steel ball (6) Check whether the amount of grease around the steel ball (6) is sufficient by raising the outer table of the carriage base block after making note of the current logic of the loading switches with "Diag-Robotics- Individually-Loading-Manual" in Test mode. Add Floil if grease is insufficient. After that, remove the side panel (right side) and cancel the operation restriction by pressing the door switch, and try manual operation of the loading mechanism. Abrasion of parts in the loading mechanism Check the number of times of operation with "Info-Run statistics- Number of times-Load/Unload" in System Administrator mode because expendable parts are included in the loading mechanism. If the number is more than 4 million, you may have to replace the carriage base. E99 loading timeover Mechanism adjustment inaccuracy Read out the current logic of the loading switches with "Diag-Robotics- Individually-Loading-Manual" in Test mode, and read out the elevating address with "Diag-Robotics- Individually-Elevation-Manual" in Test mode. Estimate the position of the carriage base block from the elevating address, and pull out the magazine to the estimated position. If the pulley or D-guide is placed against a position of the magazines such as the edge, check the adjustment of the mechanism operating unit again. Dislodged belt If the loading mechanism does not operate at all when it is located in the correct stop position, there may be trouble in the motor or the transfer system. Rotate the pulley manually, and check the change in the mechanism status. If the mechanism does not move when the pulley can be rotated, check the drive system (belt). Loading motor worn out or experiencing other trouble Check the number of times of operation with "Info-Run statictics- Number of times-Load/Unload" in System Administrator mode. If the number is more than 2 million, you may have to replace the motor assembly. There may be trouble in the motor if it can be operated by hand normally. Cancel the operation restriction by pressing the door switch and test manual operation of the loading mechanism. Abrasion of parts in the loading mechanism Check the number of times of operation with "Info-Run statictics- Number of times-Load/Unload" in System Administrator mode because expendable parts are included in the loading mechanism. If the number is more than 4 million, you may have to replace the carriage base. Demo mode preparation failure If E99 is generated when you try to carry a disc to a slot where a disc has already been set during Demo mode, check that discs are not left in improper positions. In All Slot Aging Demo mode, discs must be set in hyper magazines No. 1 to 4. The other magazines must be vacant. VD motor belt tension Install the VD motor according to the instructions. www. xiaoyu163. com QQ 376315150 9 9 2 8 9 4 2 9 8 TEL 13942296513 9 9 2 8 9 4 2 9 8 0 5 1 5 1 3 6 7 3 Q Q TEL 13942296513 QQ 376315150 892498299 TEL 13942296513 QQ 376315150 892498299 http://www.xiaoyu163.com 48. Error No. LCD Display Most Likely Causes Check Items Management Procedure E9A MTE sensor NG Disc detection sensor trouble Cancel the operation restriction by pressing the door switch, then perform disc loading/unloading operations with "Diag-Robotics- Collectively" in Test mode. It is normal if an asterisk (*) is displayed properly on the display window. If it is abnormal, perform the adjustments described in Section 6.3. If it cannot be adjusted, check that DSENS is not disconnected. EF8 MTE mecha NG Demo mode preparation failure If the error is generated during Demo mode execution, check that discs of the necessary number have been set to the specified positions. Discs must be set in hyper magazines #1 to #8 in Hyper-Drive Demo mode. Mechanism adjustment inaccuracy Read out the current logic of the loading switches with "Diag-Robotics- Individually-Loading-Manual" in Test mode, and read out the elevating address with "Diag-Robotics- Individually-Elevation-Manual" in Test mode. Estimate the position of the carriage base block from the elevating address, and pull out the magazine to the estimated position. If it seems that EF8 is generated for a slot with a disc mounted, check the adjustment of the mechanical operation system again. This error is generated only when the subsequent operation cannot be continued without opening the door, for example, when the shipping screws are in place, or after error generation. In other cases, the attempt to open the door is abandoned. Error No. LCD Display Most Likely Causes Check Items Management Procedure EF3 door open NG Something pressing against the door Check that there is nothing in front of the door to prevent it from opening. Make sure there is sufficient clearance for the door to open. Plunger trouble Execute DOOR submode in System Administrator mode and check whether the sound of pulling the plunger can be heard. If there is no sound, check the plunger drive circuit, power source, and plunger. Door lock mechanism trouble If the door does not open when the sound is heard (retried five times), there may be a trouble in the mechanical parts for releasing the door lock (such as rods and springs). Remove the panels on the left and right side, and check whether the mechanical parts for opening the door lock are mounted correctly. Door switch trouble If you see an error indication while the door is open, check the door switch mounting and the output logic. Also check the selectors of the serial system, because the door switch logic is read by converting it to serial data. E99 loading timeover Insertion error of the connector of the drive When carrying a disc to the drive, if the disc touches something while being loaded into the next bay, there may be an error mistake of the changer interface connector of the drive. Open the rear door and check the connection. The changer interface connectors can be used only for whose exclusive bays connected to the drive. If a disc remains in the drive, pull out the drive, then reconnect it properly after removing the disc. Insufficient grease around the steel ball (6) After making note of the current logic of the loading switches in Test mode (Diag → Robotics → individually → Loading → Manual,) Check whether the amount of grease around the steel ball (6) is sufficient by raising the outer table of the carriage base block. Add Floil if the amount of grease is insufficient. After that, remove the side panel (right side) and cancel the operation restriction by pressing the door switch, and try manual operation of the loading mechanism. Door-not-opening error www. xiaoyu163. com QQ 376315150 9 9 2 8 9 4 2 9 8 TEL 13942296513 9 9 2 8 9 4 2 9 8 0 5 1 5 1 3 6 7 3 Q Q TEL 13942296513 QQ 376315150 892498299 TEL 13942296513 QQ 376315150 892498299 http://www.xiaoyu163.com 49. Nonfatal errors (mainly errors with the drive unit) Confirmation of the causes and management procedure If an error is generated during initialization after resetting, the message asking you whether to continue initialization or not is displayed. If the display returns to an error message from "Initializing" again when you continue initializing by pressing the ENT key, the problem must be corrected after forcibly opening the door. If the door is opened with a disc remaining in the drive, the information as to where the disc is to be returned will be lost when the changer interface connector of the drive is disconnected. So the disc must be removed from the drive before reinstalling the drive (or reconnecting the interface connector). Pay special attention if the connection of the interface connector is loosened or it is reconnected. If an error is generated during initialization after resetting, a message asking you whether to continue initializing or not is displayed. The system switches to User mode if there is no problem other than in the device when you continue initializing by pressing the ENT key. The devices that have problems cannot be used. Error No. LCD Display Most Likely Causes Check Items Management Procedure • Dislodged or disconnect- ed connector Assy • Defective medium • Drive-circuit trouble • Check that the changer interface connector is connected. • Check that a proper medium is set in the drive. • Check whether an error message on the drive is displayed. • If the connector is disconnected or loose, reconnect it. • Replace the defective medium with a proper one. • Refer to the service manual of the drive. EB* D# setup NG EC* D# stop NG ED* E7* D# clamper NG D# clamper NG Motor or drive-circuit trouble The changer has lost data on discs in drives for some reason. When a drive was connected to the changer, the clamper of the drive was lowered. Check whether the clamper of the drive where the error was generated can be manually operated with "Diag- Robotics-Individually-Clamper- Manual" in Test mode. If it cannot be manually operated, perform the same check with the other clampers. If no clamper operates, remove the side panel (M: right side), and check the connection of the DIFB unit. Switch trouble If switching is not accomplished even though the switch is operable, check the switch and the read-in circuit of the switch. This error is generated when the clamper of the drive, which has been recognized as having no disc by the changer, is lowered. Check if a disc is loaded in the drive with a problem. If the connection is normal, also check the selector circuit. If a disc has been loaded in the drive with a problem, after the error is addressed, that disc must be retuned to the mailslot by turning off then on the power (when Hot Start is set to OFF). For this, return the disc to the original slot. If there is no disc in the drive with a problem, remove and then reinsert the drive, then initialize the unit. If you perform initialization without removing and reinserting the drive, an EF8 error will be generated. Error No. LCD Display Most Likely Causes Check Items Management Procedure EE0 hyper timeover Motor or drive-circuit trouble Check that the motor can be manually operated with "Diag- Robotics-Individually-Hyper Mag- Manual" in Test mode. If switching is not accomplished even though the switch is operable, check the switch and the read-in circuit of the switch. Dislodged or disconnected connector assembly If no operation is possible, also check the operation status of the mailslot which shares the HMIF unit using "Diag-Robotics-Individually-Mailslot- Manual." If the mailslot is also inoperable, remove the side panel (right side) and check the connection to the HMIF unit. If the connection is normal, also check the selector circuit. EE1 f-unit timeover Motor or drive-circuit trouble Check that the motor can be manually operated with "Diag- Robotics-Individually-Flip unit- Manual" in Test mode. If switching is not accomplished even though the switch is operable, check the switch and the read-in circuit of the switch. Dislodged or disconnected connector assembly If operation is not possible, also check the operation status of the clamper with "Diag-Robotics- Individually-Clamper-Manual." If the clamper is also inoperable, remove the side panel (right side) and check the connection of the DIFB unit. If the connection is normal, also check the selector circuit. Errors in the drive unit Nonfatal errors with blocks other than the drive system www. xiaoyu163. com QQ 376315150 9 9 2 8 9 4 2 9 8 TEL 13942296513 9 9 2 8 9 4 2 9 8 0 5 1 5 1 3 6 7 3 Q Q TEL 13942296513 QQ 376315150 892498299 TEL 13942296513 QQ 376315150 892498299 http://www.xiaoyu163.com 50. Error No. LCD Display Most Likely Causes Check Items Management Procedure EE9 mail timeover Motor or drive-circuit trouble Check that the motor can be manually operated with "Diag- Robotics-Individually-Mailslot- Manual" in Test mode. If switching is not accomplished even though the switch is operable, check the switch and the read-in circuit of the switch. Dislodged or disconnected connector assembly If no operation is possible, also check the operation status of the hyper magazine which shares the HMIF unit using "Diag-Robotics- Individually-Hyper Mag.-Manual." If the hyper magazine is also inoperable, remove the side panel (M: right side) and check the connection to the HMIF unit. If the connection is normal, also check the selector circuit. EF1 eeprom memory NG Memory trouble The data which may cause and error in operation are erased automatically. When mechanism initialization is completed, check "Contents" in Info submode of System Administrator mode. If all the disc detection information is "Uncertain", perform probing again in Probe submode. EF2 (Error-log only) address missing Adjustment inaccuracy Check the adjustments of the mechanical operation system and elevating speed following the descriptions in 6.2 and 6.5.(If EF2 errors are generated continuously, only the latest error remains in the Error log.) When the LEDs are lit, there may be trouble in the position sensor switch for the mail slot tray. Check the logic of SNS0, SNS1, and SNS2. EF9 EFA mail sensor NG Tray-position sensor switch trouble Check that the "MAILSLOT OCCUPIED" indication by LEDs is not lit when the mail slot is open. When the LEDs are lit, there may be trouble in the position sensor switch for the mail slot tray. Check the logic of SNS0, SNS1, and SNS2. Disc-sensor switch trouble Check that the "MAILSLOT OCCUPIED" indication by LEDs is off when you close the mail slot without setting a disc. When the LEDs are lit, and go off when you open the mailslot, there may be trouble in the disc sensor. Check the logic of SNS2. These are minor problems detected upon resetting that do not affect initialization of other mechanisms. Warning Message Check Items Fan1 stop or locked Check the operation of the fan. Fan1 connect NG Check the connection of the fan. hyper eject and insert Check whether eject/insert can be made in Hyper submode of System mode and the touch memory can be read after an insert operation. Troubles not handled as errors (warning messages) www. xiaoyu163. com QQ 376315150 9 9 2 8 9 4 2 9 8 TEL 13942296513 9 9 2 8 9 4 2 9 8 0 5 1 5 1 3 6 7 3 Q Q TEL 13942296513 QQ 376315150 892498299 TEL 13942296513 QQ 376315150 892498299 http://www.xiaoyu163.com 51. Table No. Table Operation Sequence Sequence Step Operation (hex) Step (hex) 00 Not used 00 Not used 01 Position To Element (mail slot) 00 Process for starting operation 01 Elevation to destination 02 Judging for mail opening 03 Mail open 04 Finishing process 02 Position To Element (Hypermagazine) 00 Process for starting operation 01 Elevation to destination 02 Ejecting Hypermagazine 03 Finishing process 03 Correction of MoveMedium error 00 Releasing disc 01 Finishing process 04 Releasing disc in mail 00 Waiting for address input 01 Closing mail for disc detection 02 Waiting for result of disc detection 03 Selection of operations according to result of disc detection 04 Opening mail if a disc is mounted 05 Finishing process 05 (S, D)=(Front storage, mailslot) 00 Waiting for address input 01 Closing mail for disc detection 02 Waiting for result of disc detection 03 Selection of operations according to result of disc detection 04 Opening mail if a disc is mounted 05 Waiting for key input for closing mail 06 Switching destination addresses according to result of disc detection at Storage E 07 Swinging to Storage E side 08 Elevating to Storage E 09 Disc chuck 0A Elevating to Mailslot E 0B Releasing disc 0C Waiting for result of disc detection 0D Judging for mail opening 0E Mail open 0F Finishing process 06 (S, D)=(Rear storage, mailslot) 00 Waiting for address input 01 Closing mail for disc detection 02 Waiting for result of disc detection 03 Selection of operations according to result of disc detection 04 Opening mail if a disc is mounted 05 Waiting for key input for closing mail 06 Switching destination addresses according to result of disc detection at Storage E 07 Swinging to Rear Storage E side 08 Elevating to Storage E 09 Rear disc chuck 0A Elevating to Mailslot E 0B Releasing disc 0C Waiting for result of disc detection 0D Judging for mail opening 0E Mail open 0F Finishing process 07 (S, D)=(Front storage, mailslot) 00 Waiting for address input Using Flip-box 01 Closing mail for disc detection 02 Waiting for result of disc detection 03 Selection of operations according to result of disc detection 04 Opening mail if a disc is mounted 05 Waiting for key input for closing mail 06 Switching destination addresses according to result of disc detection at Storage E 07 Checking flip-box 08 Swinging to Storage E side 09 Elevating to Storage E 0A Disc chuck and swing 0B Elevating to flip-box 0C Slide (release) 0D Flipping disc 0E Slide (chuck) and swing 0F Elevating to Mailslot E 10 Releasing disc 11 Waiting for result of disc detection 12 Judging for mail opening 13 Mail open 14 Finishing process Detailed description on error-log codes (table numbers, sequence steps) S=source, D=destination, E=element Note: The Table Number may become "00 " if an error is generated in DEMO mode. www. xiaoyu163. com QQ 376315150 9 9 2 8 9 4 2 9 8 TEL 13942296513 9 9 2 8 9 4 2 9 8 0 5 1 5 1 3 6 7 3 Q Q TEL 13942296513 QQ 376315150 892498299 TEL 13942296513 QQ 376315150 892498299 http://www.xiaoyu163.com 52. Table No. Table Operation Sequence Sequence Step Operation (hex) Step (hex) 08 (S, D)=(Rear storage, mailslot) 00 Waiting for address input corresponding to side B 01 Closing mail for disc detection 02 Waiting for result of disc detection 03 Selection of operations according to result of disc detection 04 Opening mail if a disc is mounted 05 Waiting for key input for closing mail 06 Switching destination addresses according to result of disc detection at Storage E 07 Checking flip-box 08 Swinging to Storage E side 09 Elevating to Storage E 0A Rear disc chuck 0B Elevating to flip-box 0C Slide (release) 0D Flipping disc 0E Slide (chuck) and swing 0F Elevating to Mailslot E 10 Releasing disc 11 Waiting for result of disc detection 12 Judging for mail opening 13 Mail open 14 Finishing process 09 (S, D)=(Front storage, data transmission) 00 Process for starting operation 01 Un-clamping 02 Swinging to Storage E side 03 Elevating to Storage E 04 Slide (chuck) and swing 05 Elevating to Data Transmission E 06 Slide (release) 07 Clamping disc at destination drive 08 Controlling drive (XCLMP active) 09 Finishing process 0A (S, D)=(Rear storage, data transmission) 00 Process for starting operation 01 Un-clamping 02 Swinging to Rear Storage E side 03 Elevating to Storage E 04 Slide (chuck) 05 Elevating to Data Transmission E 06 Slide (release) 07 Clamping disc at destination drive 08 Controlling drive (XCLMP active) 09 Finishing process 0B (S, D)=(Front storage, data transmission) 00 Process for starting operation Using Flip-box 01 Checking flip-box 02 Un-clamping 03 Swinging to Storage E side 04 Elevating to Storage E 05 Slide (chuck) and swing 06 Elevating to Data flip-box 07 Slide (release) 08 Flipping disc 09 Slide (chuck) 0A Elevating to Data Transmission E 0B Slide (release) 0C Clamping disc at destination drive 0D Controlling drive (XCLMP active) 0E Finishing process 0C (S, D)=(Rear storage, data transmission) 00 Process for starting operation Using Flip-box 01 Checking flip-box 02 Un-clamping 03 Swinging to Rear Storage E side 04 Elevating to Storage E 05 Slide (chuck) 06 Elevating to flip-box 07 Slide (release) 08 Flipping disc 09 Slide (chuck) 0A Elevating to Data Transmission E 0B Slide (release) 0C Clamping disc at destination drive 0D Controlling drive (XCLMP active) 0E Finishing process www. xiaoyu163. com QQ 376315150 9 9 2 8 9 4 2 9 8 TEL 13942296513 9 9 2 8 9 4 2 9 8 0 5 1 5 1 3 6 7 3 Q Q TEL 13942296513 QQ 376315150 892498299 TEL 13942296513 QQ 376315150 892498299 http://www.xiaoyu163.com 53. Table No. Table Operation Sequence Sequence Step Operation (hex) Step (hex) 0D (S, D)=(Front storage, data transmission) 00 Process for starting operation When no drive is mounted during Demo 01 Swinging to Storage E side mode 02 Elevating to Storage E 03 Slide (chuck) and swing 04 Elevating to Data Transmission E 05 Corresponding to Aging Mode (shifting return address) 06 Swinging to Storage E side (having disc) 07 Elevating to Storage E 08 Slide (release) 09 Starting controlling drive 0A Finishing process 0E (S, D)=(Rear storage, data transmission) 00 Process for starting operation When no drive is mounted during Demo 01 Swinging to Rear Storage E side mode 02 Elevating to Rear Storage E 03 Slide (chuck) 04 Elevating to Data Transmission E 05 Corresponding to Aging Mode (shifting return address) 06 Swinging to Storage E side (having disc) 07 Elevating to Storage E 08 Slide (release) 09 Starting controlling drive 0A Finishing process 0F (S, D)=(Mailslot, front storage) 00 Waiting for key input for closing mail 01 Closing mail 02 Waiting for result of disc detection 03 Selection of operations according to result of disc detection 04 Opening mail if no disc is mounted 05 Waiting for key input for closing mail 06 Switching destination addresses according to result of disc detection at Mailslot E 07 Swinging to Mailslot E side 08 Elevating to Mailslot E 09 Disc chuck 0A Elevating to Storage E 0B Releasing disc 0C Finishing process 10 (S, D)=(Mailslot, rear storage) 00 Waiting for key input for closing mail 01 Closing mail 02 Waiting for result of mail disc detection 03 Selection of operations according to result of disc detection 04 Opening mail if no disc is mounted 05 Waiting for key input for closing mail 06 Switching destination addresses according to result of disc detection at Mailslot E 07 Swinging to Mailslot E side 08 Elevating to Mailslot E 09 Rear disc chuck 0A Elevating to Rear Storage E 0B Releasing disc 0C Finishing process 11 (S, D)=(Mailslot, front storage) 00 Waiting for key input for closing mail Using Flip-box 01 Closing mail 02 Waiting for result of disc detection 03 Selection of operations according to result of disc detection 04 Opening mail if no disc is mounted 05 Waiting for key input for closing mail 06 Switching destination addresses according to result of disc detection at Mailslot E 07 Checking flip-box 08 Swinging to Mailslot E side 09 Elevating to Mailslot E 0A Disc chuck and swing 0B Elevating to flip-box 0C Slide (release) 0D Flipping disc 0E Slide (chuck) and swing 0F Elevating to Storage E 10 Releasing disc 11 Finishing process www. xiaoyu163. com QQ 376315150 9 9 2 8 9 4 2 9 8 TEL 13942296513 9 9 2 8 9 4 2 9 8 0 5 1 5 1 3 6 7 3 Q Q TEL 13942296513 QQ 376315150 892498299 TEL 13942296513 QQ 376315150 892498299 http://www.xiaoyu163.com 54. Table No. Table Operation Sequence Sequence Step Operation (hex) Step (hex) 12 (S, D)=(Mailslot, rear storage) 00 Waiting for key input for closing mail Using Flip-box 01 Closing mail 02 Waiting for result of disc detection 03 Selection of operations according to result of disc detection 04 Opening mail if no disc is mounted 05 Waiting for key input for closing mail 06 Switching destination addresses according to result of disc detection at Mailslot E 07 Checking flip-box 08 Swinging to Mailslot E side 09 Elevating to Mailslot E 0A Rear disc chuck 0B Elevating to flip-box 0C Slide (release) 0D Flipping disc 0E Slide (chuck) 0F Elevating to Rear Storage E 10 Releasing disc 11 Finishing process 13 (S, D)=(Mailslot, data transmission) 00 Process for starting operation 01 Un-clamping 02 Closing Mailslot 03 Swinging to Mailslot E side 04 Elevating to Mailslot E 05 Slide (chuck) and swing 06 Elevating to Data Transmission E 07 Slide (release) 08 Clamping disc 09 Clamp signal (XCLMP) active 0A Finishing process 14 (S, D)=(Mailslot, data transmission) 00 Process for starting operation Using Flip-box 01 Checking flip-box 02 Un-clamping 03 Closing Mailslot 04 Swinging to Mailslot E side 05 Elevating to Mailslot E 06 Slide (chuck) and swing 07 Elevating to flip-box 08 Slide (release) 09 Flipping disc 0A Slide (chuck) 0B Elevating to Data Transmission E 0C Slide (release) 0D Clamping disc 0E Clamp signal (XCLMP) active 0F Finishing process 15 (S, D)=(Mailslot, data transmission) 00 Process for starting operation When no drive is mounted during Demo 01 Closing Mailslot mode. 02 Swinging to Mailslot E side 03 Elevating to Mailslot E 04 Slide (chuck) and swing 05 Elevating to Data Transmission E 06 Corresponding to Aging Mode (shifting return address) 07 Swinging to Storage E side (having disc) 08 Elevating to Storage E 09 Slide (release) 0A Starting controlling drive 0B Finishing process 16 (S, D)=(Data transmission, front storage) 00 Process for starting operation 01 Checking if spindle stops (XSPST) 02 Swinging to Data Transmission E 03 Elevating to Data Transmission E 04 Un-clamping 05 Slide (chuck) and swing 06 Elevating to Storage E 07 Slide (release) 08 Finishing process 17 (S, D)=(Data transmission, rear storage) 00 Process for starting operation 01 Checking if spindle stops (XSPST) 02 Swinging to Data Transmission E side 03 Elevating to Data Transmission E 04 Un-clamping 05 Slide (chuck) 06 Elevating to Storage E 07 Slide (release) 08 Finishing process www. xiaoyu163. com QQ 376315150 9 9 2 8 9 4 2 9 8 TEL 13942296513 9 9 2 8 9 4 2 9 8 0 5 1 5 1 3 6 7 3 Q Q TEL 13942296513 QQ 376315150 892498299 TEL 13942296513 QQ 376315150 892498299 http://www.xiaoyu163.com 55. Table No. Table Operation Sequence Sequence Step Operation (hex) Step (hex) 18 (S, D)=(Data transmission, Front storage) 00 Process for starting operation Using Flip-box 01 Checking flip-box 02 Checking if spindle stops (XSPST) 03 Swinging to Data Transmission E side 04 Elevating to Data Transmission E 05 Un-clamping 06 Slide (chuck) 07 Elevating to flip-box 08 Slide (release) 09 Flipping disc 0A Slide and swing 0B Elevating to Storage E 0C Slide (release) 0D Finishing process 19 (S, D)=(Data transmission, rear storage) 00 Process for starting operation Using Flip-box 01 Checking flip-box 02 Checking if spindle stops (XSPST) 03 Swinging to Data Transmission E side 04 Elevating to Data Transmission E 05 Un-clamping 06 Slide (Chuck) 07 Elevating to flip-box 08 Slide (release) 09 Flipping disc 0A Slide (Chuck) 0B Elevating to Storage E 0C Slide (release) 0D Finishing process 1A (S, D)=(Data transmission, XXXX) 00 Process for starting operation When no drive is mounted during Demo 01 Stopping controlling drive mode 02 Finishing process 1B (S, D)=(Data transmission, Mailslot) 00 Process for starting operation 01 Closing Mailslot 02 Checking if spindle stops (XSPST) 03 Swinging to Data Transmission E side 04 Elevating to Data Transmission E 05 Un-clamping 06 Slide (chuck) and swing 07 Elevating to mailslot E 08 Slide (release) 09 Waiting for result of disc detection 0A Judging for mail opening 0B Opening Mailslot (only when AUTO is selected) 0C Finishing process 1C (S, D)=(Data transmission, Mailslot) 00 Process for starting operation Using Flip-box 01 Checking flip-box 02 Closing Mailslot 03 Checking if spindle stops (XSPST) 04 Swinging to Data Transmission E side 05 Elevating to Data Transmission E 06 Un-clamping 07 Slide (chuck) 08 Elevating to flip-box 09 Slide (release) 0A Flipping disc 0B Slide (chuck) and swing 0C Elevating to Mailslot E 0D Slide (release) 0E Waiting for result of disc detection 0F Judging for mail opening 10 Opening Mailslot (only when AUTO is selected) 11 Finishing process 1D Not used 00 Process for starting operation 01 Stopping controlling drive 02 Finishing process 1E (S, D)=(Front storage, front storage) 00 Process for starting operation 01 Swinging to Storage E side 02 Elevating to Storage E 03 Slide (chuck) 04 Elevating to Storage E 05 Slide (release) 06 Finishing process www. xiaoyu163. com QQ 376315150 9 9 2 8 9 4 2 9 8 TEL 13942296513 9 9 2 8 9 4 2 9 8 0 5 1 5 1 3 6 7 3 Q Q TEL 13942296513 QQ 376315150 892498299 TEL 13942296513 QQ 376315150 892498299 http://www.xiaoyu163.com 56. Table No. Table Operation Sequence Sequence Step Operation (hex) Step (hex) 1F (S, D)=(Front storage, rear storage) 00 Process for starting operation 01 Swinging to Storage E side 02 Elevating to Storage E 03 Slide (chuck) and swing 04 Elevating to Storage E 05 Slide (release) 06 Finishing process 20 (S, D)=(Rear storage, rear storage) 00 Process for starting operation 01 Swinging to Storage E side 02 Elevating to Storage E 03 Slide (chuck) 04 Elevating to Storage E 05 Slide (release) 06 Finishing process 21 (S, D)=(Rear storage, front storage) 00 Process for starting operation 01 Swinging to Storage E side 02 Elevating to Storage E 03 Slide (chuck) and swing 04 Elevating to Storage E 05 Slide (release) 06 Finishing process 22 (S, D)=(Front storage, front storage) 00 Process for starting operation Using Flip-box 01 Checking flip-box 02 Swinging to Storage E side 03 Elevating to Storage E 04 Slide (chuck) and swing 05 Elevating to flip-box 06 Slide (release) 07 Flipping disc 08 Slide (chuck) and swing 09 Elevating to Storage E 0A Slide (release) 0B Finishing process 23 (S, D)=(Front storage, rear storage) 00 Process for starting operation Using Flip-box 01 Checking flip-box 02 Swinging to Storage E side 03 Elevating to Storage E 04 Slide (chuck) and swing 05 Elevating to flip-box 06 Slide (release) 07 Flipping disc 08 Slide (chuck) 09 Elevating to Storage E 0A Slide (release) 0B Finishing process 24 (S, D)=(Rear storage, rear storage) 00 Process for starting operation Using Flip-box 01 Checking flip-box 02 Swinging to Storage E side 03 Elevating to Storage E 04 Slide (chuck) 05 Elevating to flip-box 06 Slide (release) 07 Flipping disc 08 Slide (chuck) 09 Elevating to Storage E 0A Slide (release) 0B Finishing process 25 (S, D)=(Rear storage, front storage) 00 Process for starting operation Using Flip-box 01 Checking flip-box 02 Swinging to Storage E side 03 Elevating to Storage E 04 Slide (chuck) 05 Elevating to flip-box 06 Slide (release) 07 Flipping disc 08 Slide (chuck) and swing 09 Elevating to Storage E 0A Slide (release) 0B Finishing process www. xiaoyu163. com QQ 376315150 9 9 2 8 9 4 2 9 8 TEL 13942296513 9 9 2 8 9 4 2 9 8 0 5 1 5 1 3 6 7 3 Q Q TEL 13942296513 QQ 376315150 892498299 TEL 13942296513 QQ 376315150 892498299 http://www.xiaoyu163.com 57. Table No. Table Operation Sequence Sequence Step Operation (hex) Step (hex) 26 (S, D)=(Data transmission, 00 Process for starting operation data transmission) 01 Un-Clamping 02 Checking if spindle stops (XSPST) 03 Swinging to Data Transmission E side 04 Elevating to Data Transmission E 05 Un-Clamping 06 Slide (chuck) 07 Elevating to Data Transmission E 08 Slide (release) 09 Clamping disc 0A Clamp signal (XCLMP) active 0B Finishing process 27 (S, D)=(Data transmission, 00 Process for starting operation data transmission) 01 Checking flip-box Using Flip-box 02 Un-Clamping 03 Checking if spindle stops (XSPST) 04 Swinging to Data Transmission E side 05 Elevating to Data Transmission E 06 Un-Clamping 07 Slide (chuck) 08 Elevating to flip-box 09 Slide (release) 0A Flipping disc 0B Slide (chuck) 0C Elevating to Data Transmission E 0D Slide (release) 0E Clamping disc 0F Clamp signal (XCLMP) active 10 Finishing process 28 INITIALIZE ELEMENT STATUS 00 Waiting for start of Install Aging 01 Installation Management 02 Swinging to Storage E side 03 Vertical movement to address for installation 04 Ejecting disc (storage → carriage) 05 Collecting data on whether a disc is mounted 06 Returning disc (carriage → storage) 07 Waiting for completion of Install Aging 29 EXCHANGE MEDIUM (Not used) - - 2A Not used - - 2B Drive Hotline Check - - 2C Step Mode: Ejecting disc from rack 00 Designating VDEST address transformed from VMMSOURCE address (rack #) 01 Elevating to designated address 02 Chucking disc on rack side 03 Transforming VMMSOURCE address to VDEST address (mail or drive) 04 Swinging to flipped side 05 Elevating to flip-box 06 Releasing disc to Mail or Drive 07 Flipping at flip-box 08 Chucking disc on rack side 09 Transforming VMMSOURCE address to VDEST address (mail or drive) 0A Swinging to drive side (only when Drive is designated at 03) 0B Elevating to designated address 0C Releasing disc to Mail or Drive 0D Clamping disc or opening mail 0E Starting driving (only when a drive is mounted) 2D Step Mode: Returning disc to rack 00 Dummy step 01 Dummy step 02 Releasing disc to rack 03 Elevation of carriage base 04 Swinging to drive side (only when Drive is designated) 05 Transforming VMMSOURCE address to VDEST address (rack #) 06 Chucking disc on rack 07 Flipping at flip-box 08 Releasing disc to Mail or Drive 09 Elevating to flip-box 0A Swinging to flipped side 0B Transforming VMMSOURCE address to VDEST address (rack #) 0C Chucking disc in drive or mail 0D Releasing clamped disc or closing mail 0E Stopping driving (only when a drive is mounted) 2E Elevation aging 00 Initial setting for aging 01 Elevating carriage base to #212 02 Descending carriage base to #1 03 Checking conditions for finishing aging www. xiaoyu163. com QQ 376315150 9 9 2 8 9 4 2 9 8 TEL 13942296513 9 9 2 8 9 4 2 9 8 0 5 1 5 1 3 6 7 3 Q Q TEL 13942296513 QQ 376315150 892498299 TEL 13942296513 QQ 376315150 892498299 http://www.xiaoyu163.com 58. Table No. Table Operation Sequence Sequence Step Operation (hex) Step (hex) 2F Loading aging 00 Initial setting for aging 01 Loading 02 Returning 03 Checking conditions for finishing aging 30 Flip aging 00 Initial setting for aging 01 Flipping 02 Flipping again 03 Checking conditions for finishing aging 31 Mailslot aging 00 Initial setting for aging 01 Opening mail 02 Closing mail 03 Checking conditions for finishing aging 32 Hyper aging 00 Initial setting for aging 01 Hyper eject 02 Hyper insert 03 Checking conditions for finishing aging 33 Initializing mechanism ==== Initializing mechanism ==== 00 Waiting for a disc moving to safe position for loading 01 Closing Mailslot 02 Initializing elevation mechanism ==== Returning disc to carriage mechanism ==== 03 Checking if a disc is on carriage mechanism 04 Swinging to return (Storage) E side 05 Vertical movement to address for returning disc 06 Returning disc ==== Returning disc to drive ==== (including returning disc to flip-box) 07 Closing if aging return by Clamper-Open switch not supported 08 Disc detection at data-transmission E 09 Swinging to Storage E side A Vertical movement to address for returning disc B Loading disc at address for returning disc C Checking if address for returning disc is vacant D Ejecting existing disc at address for returning disc E Swinging to data-transmission E side F Vertical movement to data-transmission E 10 Horizontal check for flipping, and for drive, clamping after disc insertion 11 Pulling and flipping disc and remounting into drive 12 Switching destinations depending on whether a disc mounted or not at returning address 13 Vertical movement to address for returning disc 14 Returning disc 15 Disc detection at data-transmission E whether disc is mounted ==== Finishing process ==== 16 Swinging to return (storage) E side 17 Elevating to #3 18 Process for finishing initialization ==== Auxiliary operation for returning disc ==== 19 Swinging to return (storage) E side 1A Elevating to Mailslot (Return address=Mailslot) 1B Closing Mailslot 1C Waiting for decision of whether a disc is in mail 1D Switching destinations depending on whether a disc is in mail 1E Opening Mailslot 1F Waiting for key input for closing Mailslot 20 Judging if disc in mail 21 Releasing disc into Mailslot 22 Judging if disc in mail ==== Start playing disc ==== 23 from ALLCLCW(7) to INIE(16h) ==== Flipping disc ==== 24 Swinging to Data Transmission E side 25 from BRAINITA(12h) to BRAINITA(12h) 26 Checking flip-box 27 Slide (release) 28 Flipping disc 29 Checking returning address again 34 00 Request to stop drive 01 Checking if drive stops 02 Process for finishing initializing www. xiaoyu163. com QQ 376315150 9 9 2 8 9 4 2 9 8 TEL 13942296513 9 9 2 8 9 4 2 9 8 0 5 1 5 1 3 6 7 3 Q Q TEL 13942296513 QQ 376315150 892498299 TEL 13942296513 QQ 376315150 892498299 http://www.xiaoyu163.com 59. Physical Addresses FRONT REAR address(hex) address(hex) address(hex) address(hex) Magazine Magazine Drive Flip D4 Hyper D4 CD Drive 8 C1 Magazine 7 B8 Flip AC Mail B2 Drive 7 A3 9E 9E 97 Drive 6 Magazine Magazine 3 6 82 Flip 7C Drive 5 6D 6D 68 68 61 Drive 4 Magazine Magazine 2 5 4C Flip 46 Drive 3 37 37 32 32 2B Drive 2 Magazine Magazine 1 4 16 Flip 10 Drive 1 1 1 www. xiaoyu163. com QQ 376315150 9 9 2 8 9 4 2 9 8 TEL 13942296513 9 9 2 8 9 4 2 9 8 0 5 1 5 1 3 6 7 3 Q Q TEL 13942296513 QQ 376315150 892498299 TEL 13942296513 QQ 376315150 892498299 http://www.xiaoyu163.com 60. SCSI SENSE CODE Sense Key Generic Category Description 0h NO SENSE Indicates that there is no specific sense key information to be reported for the designated logical unit. This would be the case for a successful command. 2h NOT READY Indicates that the drive cannot be accessed. Operator intervention may be required to correct this condition. 4h HARDWARE ERROR Indicates that the device detected a non-recoverable hardware failure while performing the command or during a self test. 5h ILLEGAL REQUEST Indicates that there was an illegal parameter in the CDB or in the additional parameters supplied as data for some commands. If the device detects an invalid parameter in the CDB, then it terminates the command without altering the medium. If the device detects an invalid parameter in the additional parameters supplied as data, then the device may have already altered the medium. 6h UNIT ATTENTION Indicates that the removable medium may have been changed or the device has been reset. Bh ABORTED COMMAND Indicates that the device has aborted the command. The Host may be able to recover by trying the command again. This error is reported for conditions such as an overrun etc.. Sense Key ASC-ASCQ Description 0h (NO SENSE) 00-00 No additional sense information 2h (NOT READY) 04-01 In process of becoming ready 04-02 Initializing command required 04-03 Manual intervention required 04-80 Waiting for preparations 3A-00 Medium not present 53-80 Medium release is impossible 53-82 Door is open 53-83 Disc mounted incorrectly 53-86 Denied by the current function settings 53-88 Medium removal prevented 4h (HARDWARE ERROR) 15-01 Mechanical positioning error 40-NN Diagnostic failure on component NN (80h-FFh) 43-00 Message error 49-00 Invalid message error 5h (ILLEGAL REQUEST) 20-00 Invalid command operation code 21-00 Element address is out of range in CDB 21-01 Invalid element address 24-00 Invalid field in CDB 25-00 Logical unit is not supported 26-00 Invalid field in parameter list 39-00 Saving parameters is not supported 3B-0D Destination element full 3B-0E Source element empty 3B-11 Medium magazine not accessible 3B-80 Medium transport element is full 6h (UNIT ATTENTION) 28-01 Import or export element accessed 29-00 Power on, reset or bus device reset occurred 2A-01 Mode parameter is changed Bh (ABORTED COMMAND) 47-00 SCSI parity error 48-00 Initiator detected error message received 53-81 Someone improperly opens the door 53-84 Source storage element overlap 53-85 Invalid source storage element address 53-87 Non-volatile information is invalid Sense Key ASC / ASCQ www. xiaoyu163. com QQ 376315150 9 9 2 8 9 4 2 9 8 TEL 13942296513 9 9 2 8 9 4 2 9 8 0 5 1 5 1 3 6 7 3 Q Q TEL 13942296513 QQ 376315150 892498299 TEL 13942296513 QQ 376315150 892498299 http://www.xiaoyu163.com 61. CHANGER DIAGNOSIS PROGRAM “Diagnose V” How to acquire information on the internal system of the changer, how to upgrade the firmware, and how to modify information on the internal system of the changer are outlined here. For details, refer to the user's manual for Diagnose V. After the program is started, the above main display appears, and indications for the SCSI devices being connected to the PC are displayed. Note: If the Automatic Insertion function for drives is set to ON in the settings made on the PC, when the program starts, it asks if you wish to turn this function OFF. In this case, set this function to OFF. • Diagnose button Click on this button to read the EEPROM of the changer to display information on the internal system of the changer. • Save button Click on this button to save the information on the internal system of the changer as a file. 1. Main display 2. Acquiring information on the internal system of the changer • Example of results of a diagnosis www. xiaoyu163. com QQ 376315150 9 9 2 8 9 4 2 9 8 TEL 13942296513 9 9 2 8 9 4 2 9 8 0 5 1 5 1 3 6 7 3 Q Q TEL 13942296513 QQ 376315150 892498299 TEL 13942296513 QQ 376315150 892498299 http://www.xiaoyu163.com 62. With Diagnose V, Version 2.50 and afterwards, content of the firmware of the changer can be rewritten. Designate a file to which you wish the firmware to be rewritten with the Select button, then click on the Update button. If the MMCB Unit is replaced for a repair, etc., the serial number of the changer must be reentered. On the main display, select "Changer" (the line on the display is reversed,) then click on the Option button. Enter the serial number of the changer, then click on the Set button. Click on the OK button. After upgrading is completed, restart Diagnose V to display the upgraded version of the program. 3. Upgrading the firmware 4. Modification of the information on the internal system of the changer www. xiaoyu163. com QQ 376315150 9 9 2 8 9 4 2 9 8 TEL 13942296513 9 9 2 8 9 4 2 9 8 0 5 1 5 1 3 6 7 3 Q Q TEL 13942296513 QQ 376315150 892498299 TEL 13942296513 QQ 376315150 892498299 http://www.xiaoyu163.com 63. www. xiaoyu163. com QQ 376315150 9 9 2 8 9 4 2 9 8 TEL 13942296513 9 9 2 8 9 4 2 9 8 0 5 1 5 1 3 6 7 3 Q Q TEL 13942296513 QQ 376315150 892498299 TEL 13942296513 QQ 376315150 892498299 http://www.xiaoyu163.com
版权声明
1. 本站所有素材,仅限学习交流,仅展示部分内容,如需查看完整内容,请下载原文件。
2. 会员在本站下载的所有素材,只拥有使用权,著作权归原作者所有。
3. 所有素材,未经合法授权,请勿用于商业用途,会员不得以任何形式发布、传播、复制、转售该素材,否则一律封号处理。
4. 如果素材损害你的权益请联系客服QQ:77594475 处理。